2024 CFSEI DESIGN EXCELLENCE AWARD WINNERS
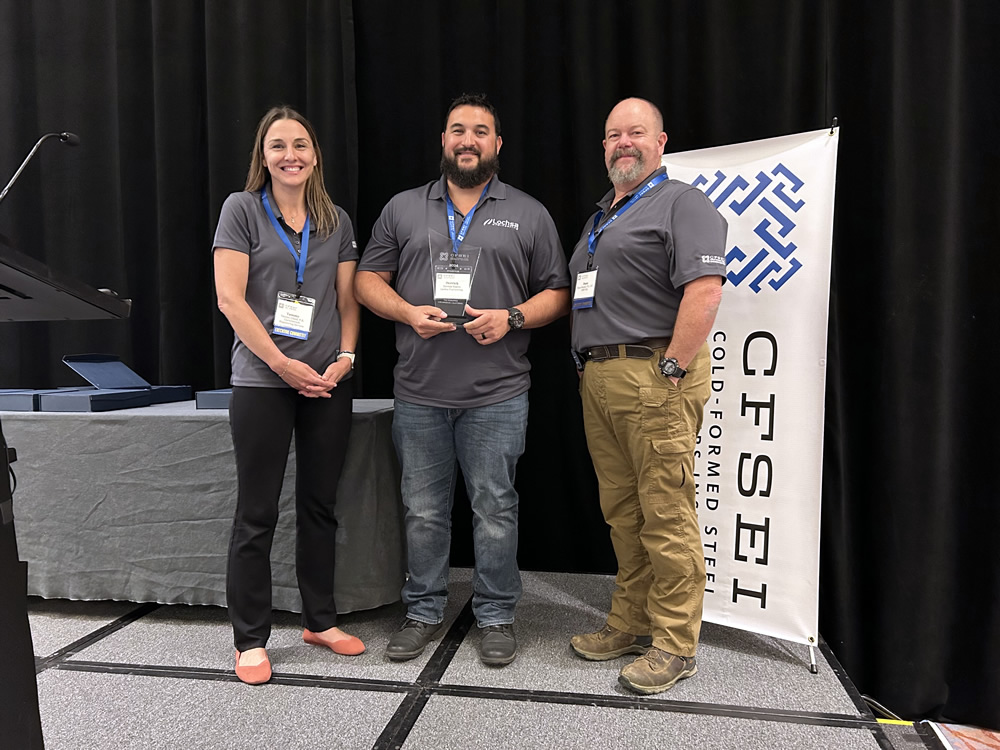
FIRST PLACE
LOCHSA ENGINEERING, LLC THE (W)RAPPER LOS ANGELES, CALIFORNIA
The (W)rapper 5790 West Jefferson Blvd. Los Angeles, CA 90016
Completion Date: January 2023
Owner: Samitaur Constructs. Architect of Record: Eric Owen Moss, Eric Owen Moss Architects. Engineer of Record for Structural Work: Atka Zekioglu, ARUP. Cold-Formed Steel Specialty Engineer: Derrick Suarez, P.E., Lochsa Engineering, LLC. Cold-Formed Steel Specialty Contractor: Trevor Lykins, Performance Contracting, Inc. Award Entry Submitted by: Nick Hrico, P.E., Lochsa Engineering, LLC.
Project Background
The (W)rapper Building stands as a testament to technical innovation and creative design, soaring 235-feet high with 7 stories dedicated to fostering creativity and innovation among professionals and forward-thinking enterprises.
The building’s title, (W)rapper, encapsulates its dual significance. When the “W” is included, it forms “Wrapper,” reflecting the structure’s enveloping and pioneering design. Without the “W,” the title transforms into “Rapper,” paying homage to the vibrant musical heritage of South-Central Los Angeles where the tower stands.
Notably, the (W)rapper defies convention by avoiding typical columns and rows found in most high-rise buildings. Instead, it showcases a network of curving bands skillfully engineered to wrap around the structure, originating from several geometric center points. This technical feat exemplifies the best practices in the use of cold-formed steel (CFS), setting a new standard for what is achievable in CFS engineering and design.
The (W)rapper’s distinctive form stands as a testament to the ingenuity and advanced engineering skills required to achieve such a groundbreaking and innovative design. The tower’s construction was not without its share of challenges. The exceptional skills and expertise of Lochsa’s engineers played a pivotal role in overcoming and ensuring the project’s success.
Design Challenges and Solutions
Hyperbolic Walls #1: Exterior and interior wall systems that are complex cold-formed steel (CFS) trusses that curve/radius in multiple directions. At the exterior walls, the framing bypassed the second level while also attaching to the underside of the slab.
All attachments had to be resilient to support the design loads while being flexible enough to account for anticipated horizontal and vertical deflections of the base structure.
The high seismicity of the project location created large lateral design loads and building movement to be accounted for to properly design these trussed walls, Finite Element Software was needed to accurately portray the exact design conditions and outcomes of the CFS members and connections efficiently.
Standard hand-calculations and typical industry CFS Design Software were not able to be used. In addition to the modeling software used for member design, Radiustrack Corporation played a large role in helping model the fabrication of the CFS truss members for PCI and the design team. (ref. Sheet LG3.21).
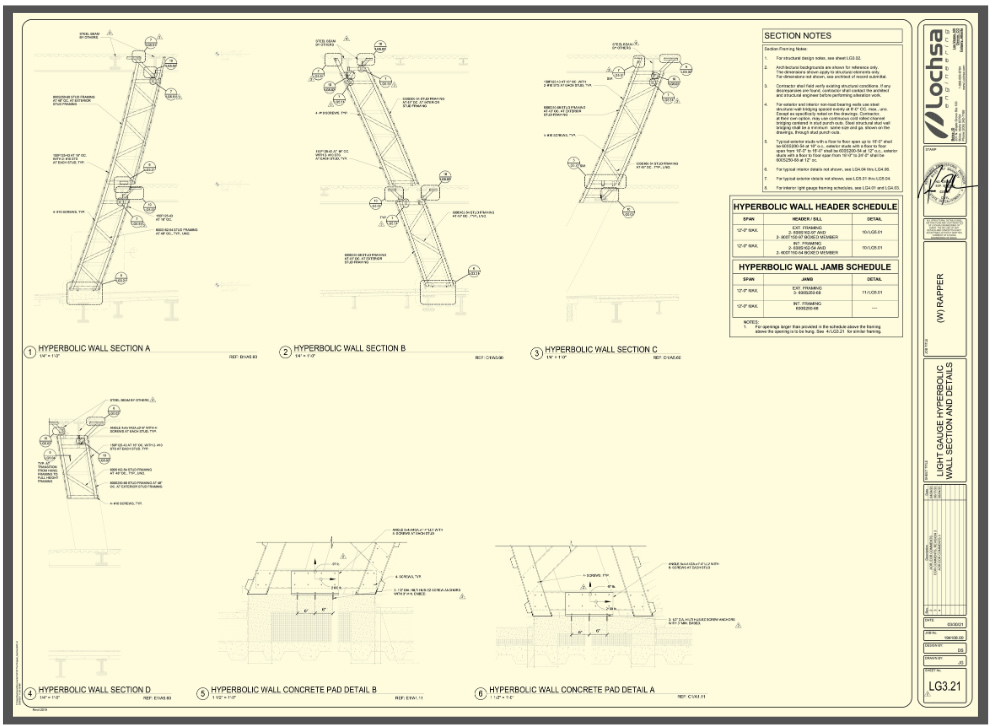
Stair #2: This stair system was unique in that it cantilevers from the base building creating an exposed condition to wind/extreme seismic loads and adverse weather.
The exterior CFS framing members that wrapped the stairs needed to be intricately designed as a finite element system for proper load resistance fire rating and weather proofing. To solve this, the design team used Finite Element Software to aid in developing unique CFS detailing/connections that were integrated with the complex base building steel framing for these egress elements. (ref. Sheets LG3.02 and LG5.53).
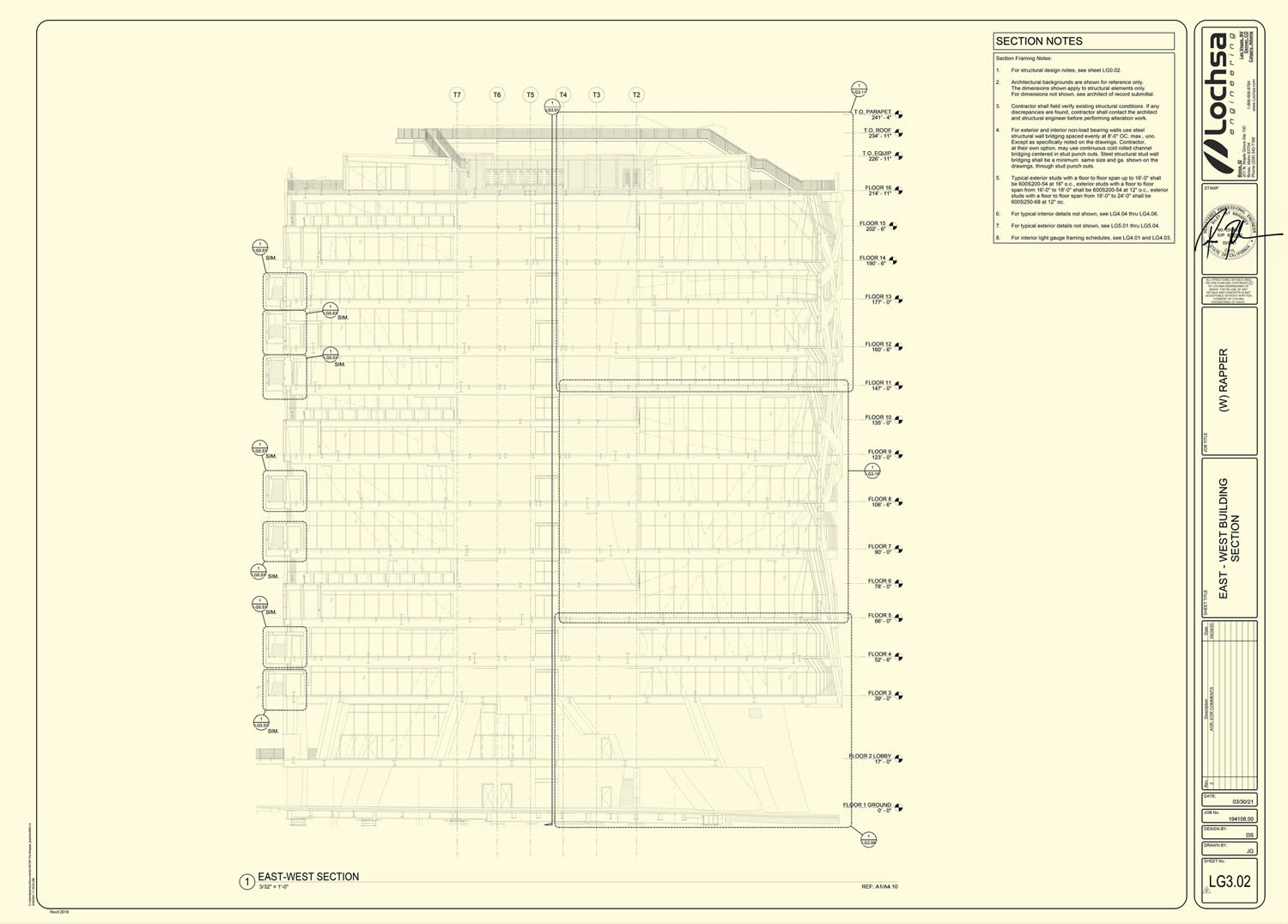

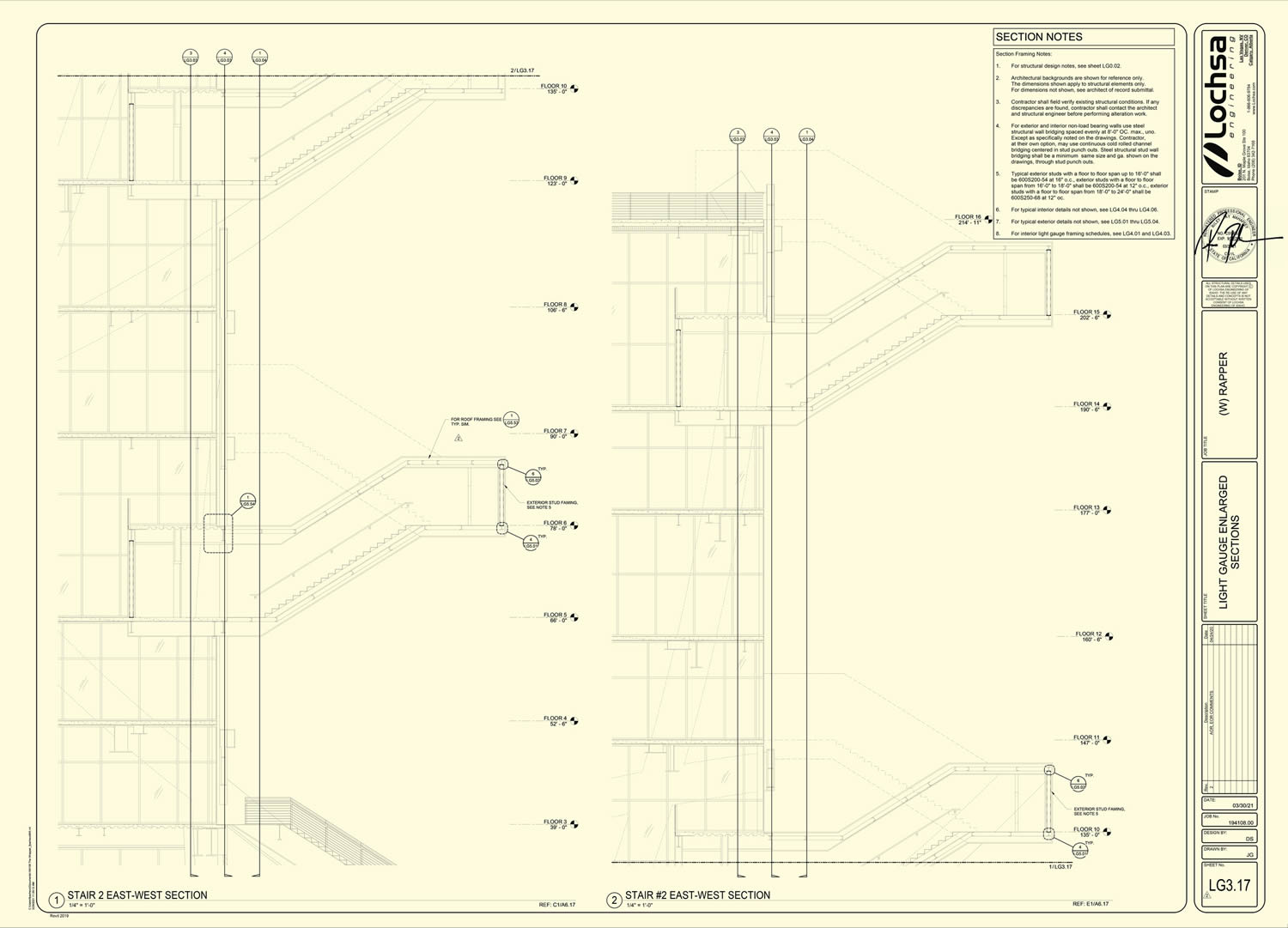
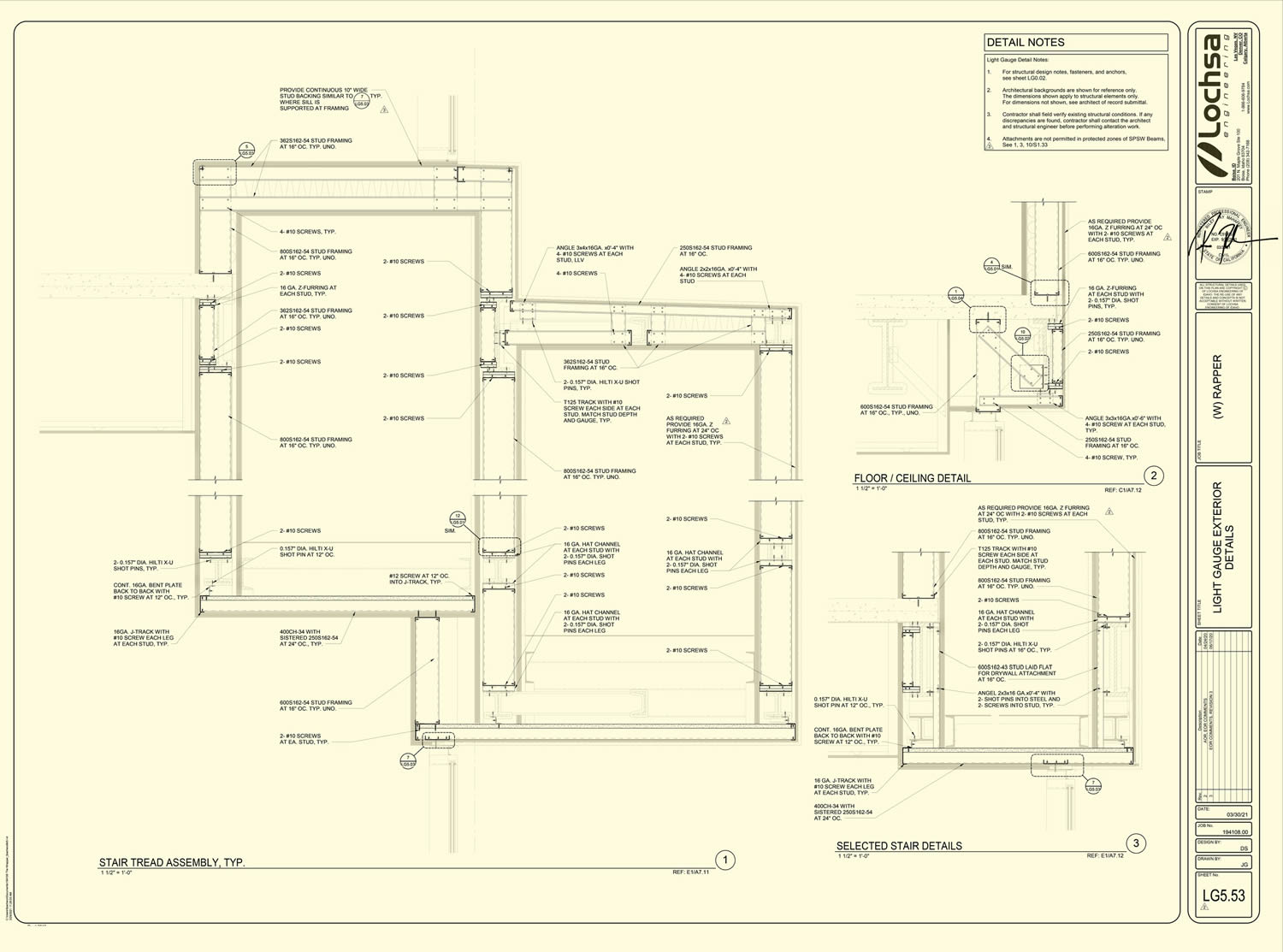
Tower Windows #3: The tower elevations were required to maintain similar architectural elevation looks as the main part of the building to create the theme of The (W)rapper. Most of the windows in these elevations matched that aesthetic.
The unique headers and jambs were at varying angles rather than straight vertical and horizontal that are accustomed typical construction. Corner conditions required the window systems to “wrap” the building at 90-degree angles. This condition required a cantilevered “knee” or low wall design condition to support the window system.
The most difficult windows wrapped corners and had typical CFS wall systems above and below the openings within the same level. To properly design these areas, Finite Element Software was needed to accurately portray the exact design conditions and outcomes of the CFS members and connections efficiently.
Standard hand-calculations and typical industry CFS Design Software were not able to be used. (ref. Sheet LG2.03).
Lastly, to accurately address the three (3) design challenges and solutions, the use of CFS framing strongly aided in the proper, effective design and constructability of the locations.
The efficiency of the material to resist the future gravity/lateral loadings, required fire ratings and aid in strict deflection level adherence was perfect.
Harmonized connections were also created that allowed for the elaborate finish support system to perform properly on the unique base structure.
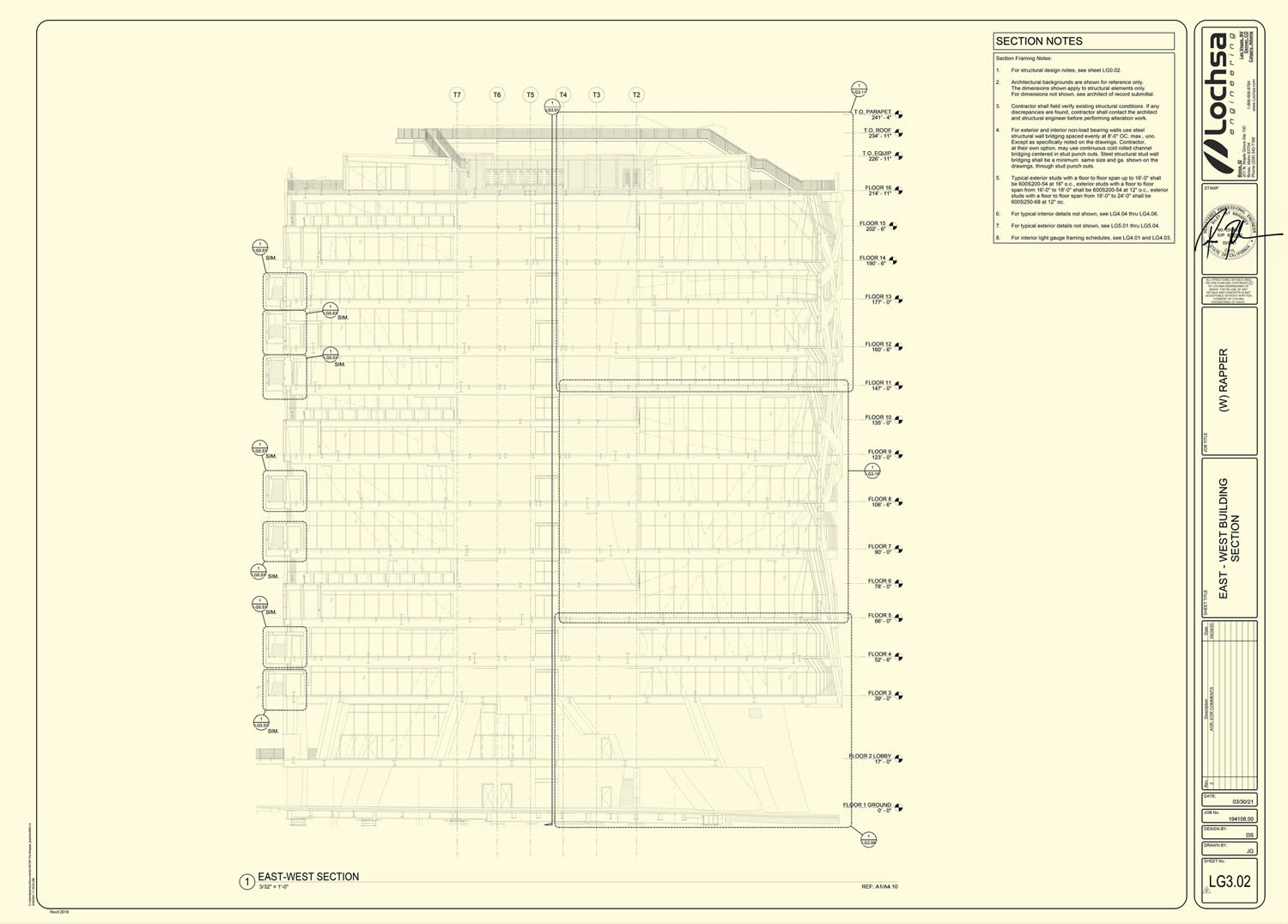
|