2024 CFSEI DESIGN EXCELLENCE AWARD WINNERS
HONORABLE MENTION
MCCLURE ANGELO CAPUTO’S – NORRIDGE NORRIDGE, ILLINOIS
Angelo Caputo’s – Norridge 4410 North Harlem Avenue Norridge, IL 60706
Completion Date: 2023
Owner: Caputo’s Architect of Record: Camburas and Theodore Architects. Engineer of Record for Structural Work: Camburas and Theodore Architects. Cold-Formed Steel Specialty Engineer: Josh Garton, P.E., McClure. Cold-Formed Steel Specialty Contractor: Austin McInerny, Radius Track Corporation; Sara Gutowski, Radius Track Corporation; Carl Wedell, Radius Track Corporation. Installing Contractor: Bill Becker, TIDAL Construction Services, Inc. General Contractor: John Divita, J. Divita & Associates-Lake Zurich. Award Entry Submitted by: Lauren Gutknecht, McClure.
Project Background
McClure’s scope involved the design of cold-formed steel (CFS) prefabricated panels at the entryway of Angelo Caputo’s in Norridge, Illinois, focusing on CFS doubly curved panels, spanning between structural steel with a compound mitered connection to the structural steel. The project showcases McClure’s expertise in innovative engineering solutions for challenging structural designs.
Design Challenges and Solutions
McClure was tasked with designing 3,000 square feet of roof panels, 1,000 square feet of exterior soffit panels and 2,000 square feet of interior field-framed soffit framing. These elements presented several challenges, including complex geometry, load requirements and integration with other building systems. The roof panels needed to support typical ASCE 7 loads for roofs (dead, live, snow and wind) as well as an increased 30psf roof live load.
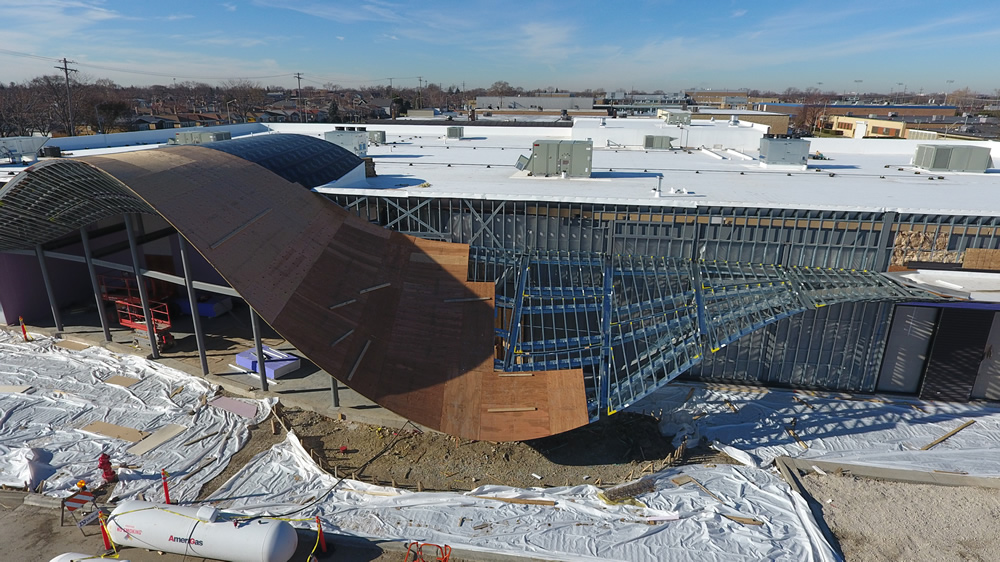
Each panel is comprised of two curved beams spanning between structural steel roof beams, with roof joists spanning in the opposite direction. Each prefabricated panel had to drop geometrically between the steel layers.
Due to the doubly curved nature of the finish geometry, the straight wide-flanged steel beams height and location had significant variation in the height relative to the panel location. The variation created conditions where the CFS beams would require connections above, below and in the middle of the wide flange beams and would require panel support points past the extent of each beam.
To resolve these issues, the CFS panels were prefabricated by Radius Track. To create the connection points, the design included the following beam attachments:
- Attachments above beams: Braced cantilevers were installed on top of each beam to set the top of the roof panels.
- Attachments to the face of beams and where the beams clashed with the wide flange beams: Vertical tracks were clipped to the wide flange beams to create attachment surfaces.
- Attachments below the beams for soffits: Braced cantilevers downward and stud segments infilled between structural steel layers.
This panelized system with integrated beams allowed for fewer, though more robust, field connections and expedited the installation process. Fewer connection points on a curved panel also expedited the set time, as each joist did not require being field-located in 3D space.
The interior ceiling used radiused studs at 4-feet o.c., with radiused hat channels to create a two-way system with discrete hanging points. To prevent an additional load from hanging off the roof system, McClure specified that an additional joist be added between the steel – a secondary support system for this additional scope of framing.
This detailing approach combined with the prefabrication, BIM and coordination created a rapid installation and a bold and unique structure for the owner.
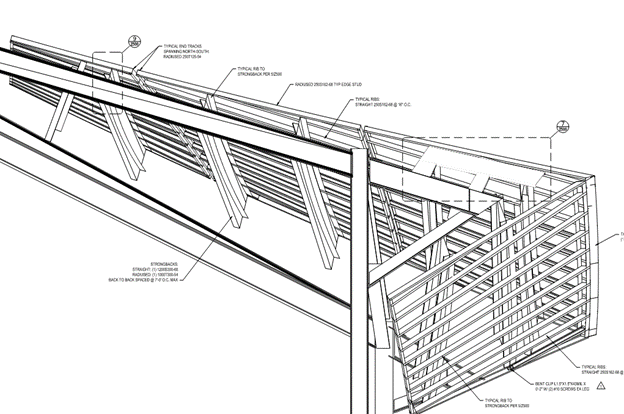
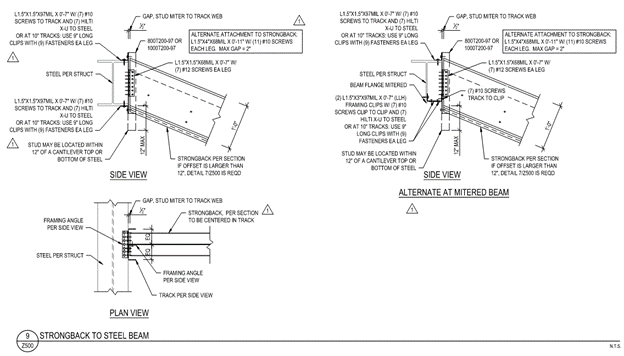
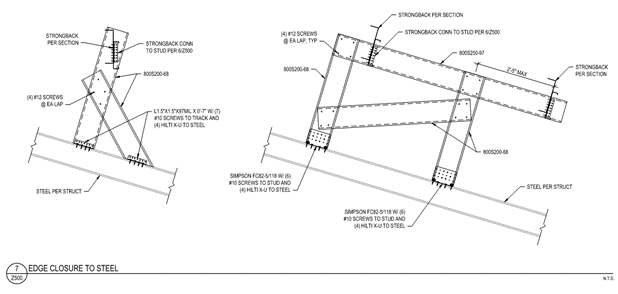
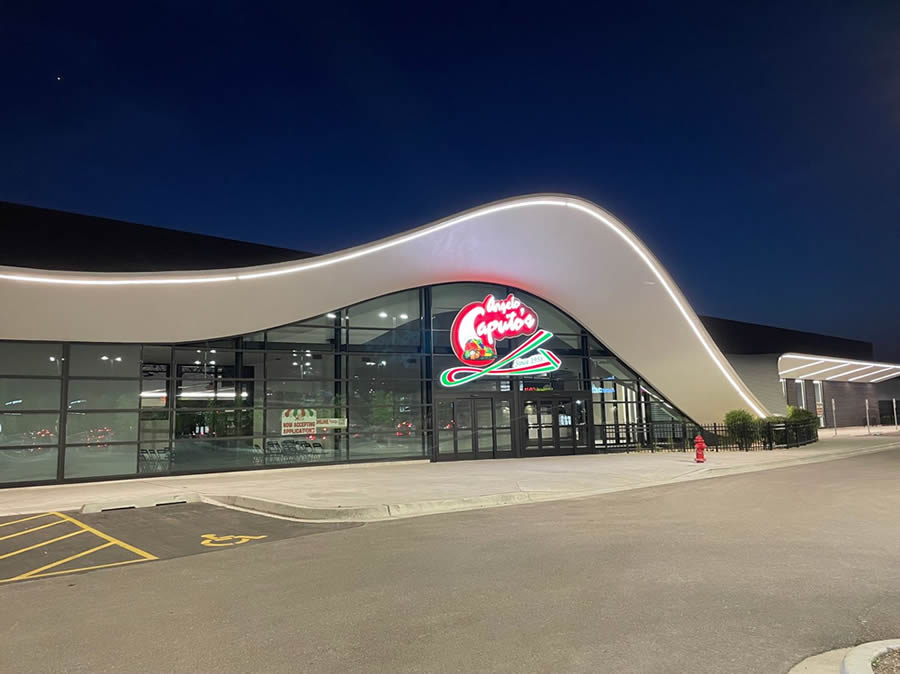
|