2025 CFSEI DESIGN EXCELLENCE AWARD WINNER
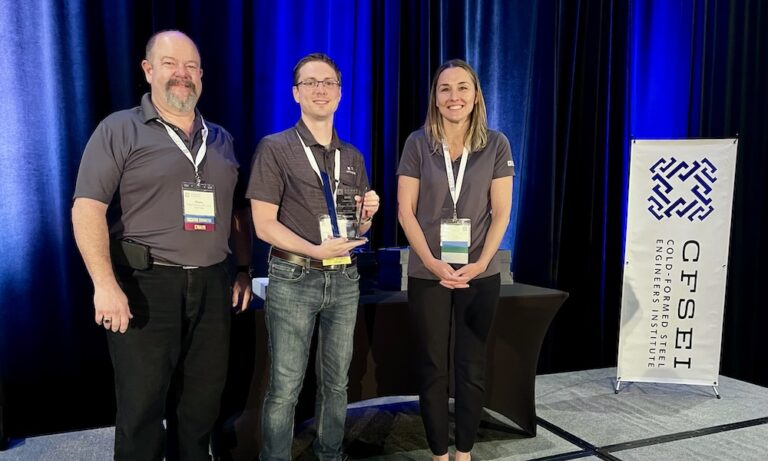
FIRST PLACE - RESIDENTIAL/HOSPITALITY
McCLURE - RANCHO MONTE ALEGRE CARPINTERIA, CALIFORNIA
Rancho Monte Alegre 1937 Monte Alegre Drive Carpinteria, California 93013
Completion Date: 2024
Owner: Johnson Residence. Architect of Record: Robert Donaldson III, Shubindonaldson Architects. Engineer of Record for Structural Work: R. Paul Belmont, Ashley & Vance Engineering, Inc. Cold-Formed Steel Specialty Engineer: Josh Garton, P.E., S.E., McClure. Cold-Formed Steel Specialty Contractor: Jeff Montague, Radius Track. Award Entry Submitted by: Lauren Gutknecht, McClure.
Project Background
Exterior double curved cold-formed steel (CFS) custom fabricated tabbed box assemblies supported off a two-story residential structure. The project featured a modernist curved façade and a combination of wood framing and CFS elements. While much of the building is wood-framed, the exterior includes predominantly non-bearing CFS panels with select load-bearing sections where necessary.
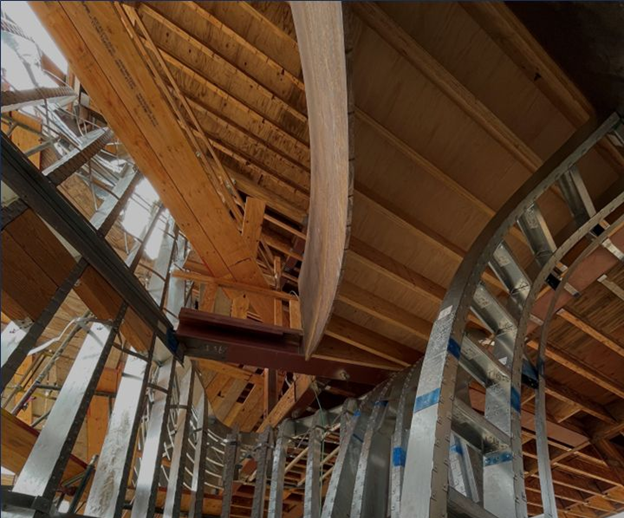
Design Challenges and Solutions
Design Complexity and Geometry: The design called for a complex, curved façade that wraps around both the interior and exterior, creating continuously varying surfaces. The initial proposal involved laser-cut plywood grids, but that approach proved unfeasible. A custom CFS solution emerged to handle the doubly curved geometry.
The most unusual challenge was that the interior and exterior planes of the walls diverged, causing the CFS studs to vary in depth along their height. Additionally, the wall finishes were not perpendicular to one another. So the CFS box assemblies—formed from individual flat plates to make the webs and flanges—took on parallelogram shapes, rather than the standard rectangular cross-sections, while accommodating doubly curved surfaces.
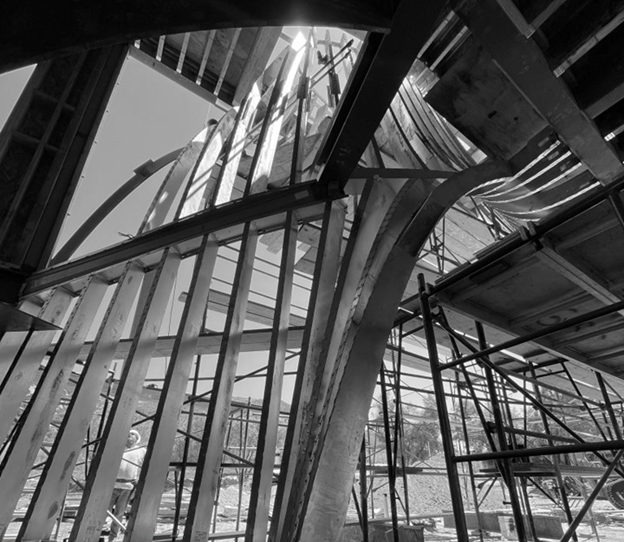
Custom Laser-Cut Box Assemblies: To achieve the required curvature, custom-fabricated tabbed box assemblies were laser-cut from flat sheet steel. Each piece was designed with pre-punched tabs and holes, allowing them to be riveted together. This method effectively created self-jigging assemblies: as the tabs were connected to matching holes, the shape naturally formed the intended arc.
An extensive engineering evaluation was required to verify that these components could handle shear, axial loads, torsional demands and biaxial bending moments. The analysis included finite element modeling, rational structural design checks and careful application of American Iron and Steel Institute (AISI) specifications for CFS—even though these unique shapes were not addressed by standard design guides.
This complex design was accommodated by transferring the stud model from Rhino to RISA for structural analysis. The force results were post-processed in Excel using the RSG CFS plugin to allow for custom shape analysis and AISI code checks.
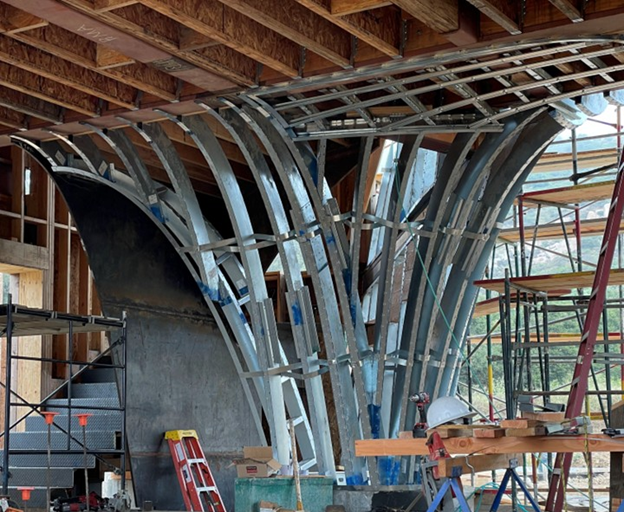
Structural Movement and Load Transfer: The doubly curved surfaces necessitated complex movement joints that allowed gravity loads to be transferred at the mid-level floor, with the ceiling, soffit and lower walls suspended from below and the upper walls slipped at the roof. This sequencing of load transfer was critical for avoiding unsightly expansion joints that would have compromised the architectural vision. Through careful coordination, the design team enabled the entire assembly to accommodate structural movement while maintaining the façade’s uninterrupted, curvilinear appearance.
Load-Bearing Adaptation Originally conceived as a non-bearing wall system, the CFS assemblies also had to accommodate unexpected gravity loads near the stair framing. The cramped area around the stair core left no room for separate support columns or beams, so the CFS assemblies were reconfigured to include a narrower, straight box beam placed between the principal steel columns. This modification permitted the framing to carry the necessary stair loads without altering the overall geometry.
Conclusion
Rancho Monte Alegre exemplifies how CFS can be adapted to serve both architectural ambition and rigorous structural demands. From first-of-its-kind, laser-cut tabbed boxes accommodating doubly curved walls, to the careful integration of movement joints and load-bearing modifications, the project demonstrates an approach to shaping metal that extends beyond standard CFS design practices. The result is a modernist, curved structure that blends structural precision with a unique architectural form.
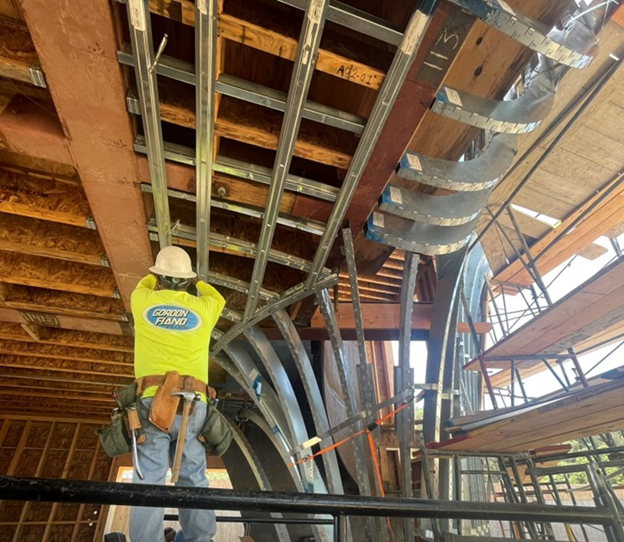
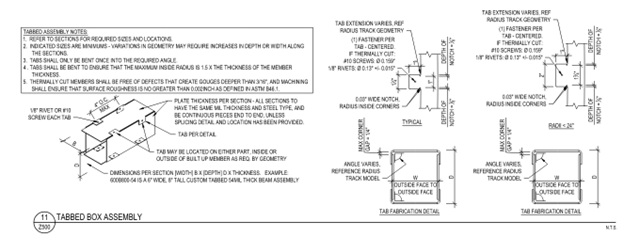
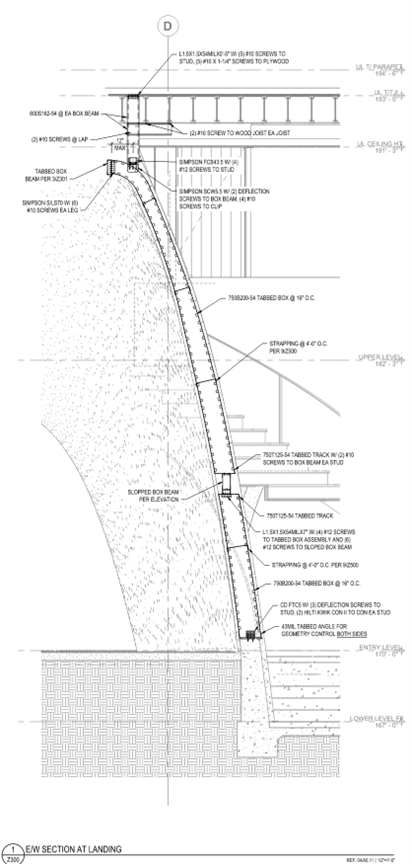
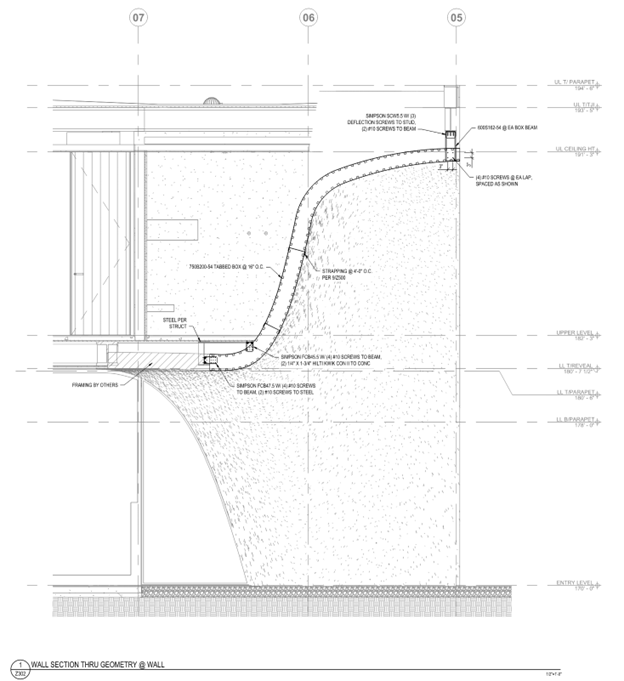
|