2025 CFSEI DESIGN EXCELLENCE AWARD WINNER
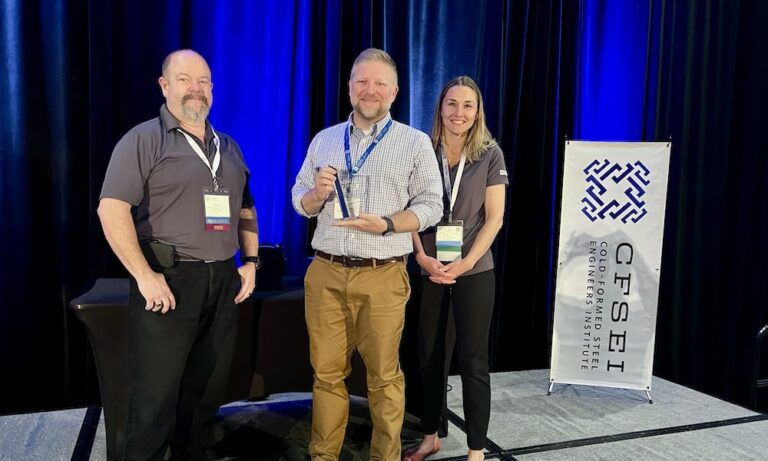
SECOND PLACE - RESIDENTIAL/HOSPITALITY
EXCEL ENGINEERING, INC. AND SK&A STRUCTURAL ENGINEERS BANNER LANE (FORMERLY SURSUM CORDA) WASHINGTON, DISTRICT OF COLUMBIA
Banner Lane (Formerly Sursum Corda) 1112 First Terrace NW Washington, District of Columbia 20001
Completion Date: November 2023 Construction Cost: $220 million
Owner: Toll Brothers. Architect of Record: Ingrid Marrone, WDG Architecture. Engineer of Record for Structural Work: Hakan Onel, P.E., S.E., SK&A Structural Engineers. Cold-Formed Steel Specialty Engineer: John Parish, Excel Engineering, Inc. Cold-Formed Steel Specialty Contractor: Matt Longberry, Div005, Daniel Miller, Panel Systems, Inc. Award Entry Submitted by: Joseph Uchno, SK&A Structural Engineers.
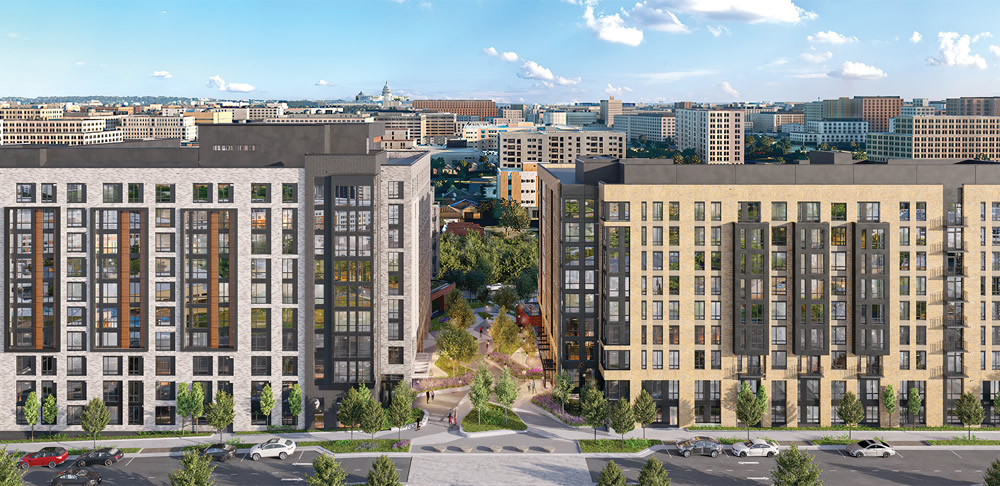
Project Background
Originally named Sursum Corda after the Washington, DC neighborhood in which it resides, the Banner Lane Apartments comprise two residential towers with a total of 561 units, including 118 designated as affordable housing. The project encompasses 726,900 square feet and is supported by a common ground-level podium and two levels of below-grade parking. The podium consists of a thick concrete transfer slab that supports the two towers above. The southwest tower rises nine stories, while the southeast rises ten, both constructed with CFS steel (CFS) stud bearing walls.
The floor system between bearing walls features a 3" composite metal deck topped with 2 1/2" of lightweight concrete. Lateral loads are resisted by CFS flat strap braces applied to select metal stud walls. The building façade is primarily brick, with punched windows and metal panel accents. Amenities include a swimming pool, one acre of outdoor public space, fitness areas, yoga and cycling rooms and a greenhouse with a gardening station. Due to the scale of the project, two CFS suppliers were engaged—one for each tower.
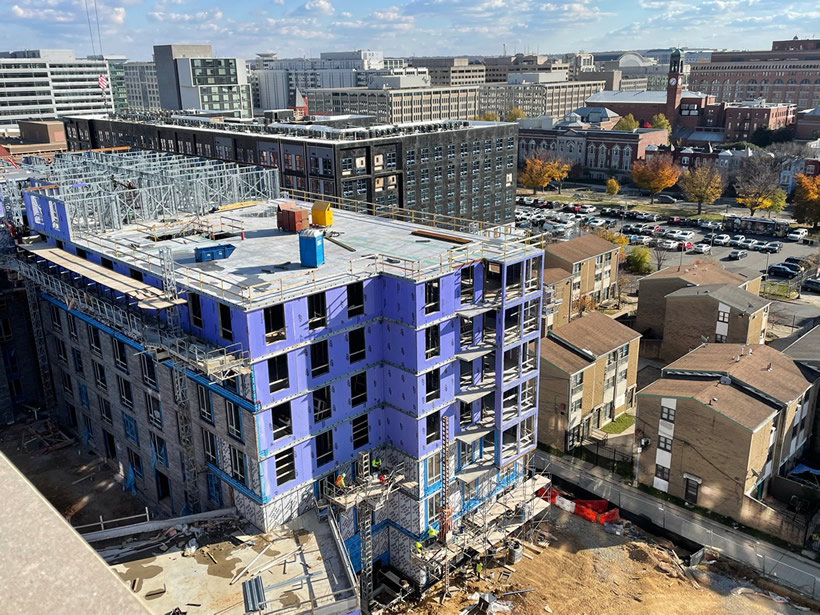
Design Challenges and Solutions
A development of this size, with a maximum of 10 levels supported by the CFS metal studs, pushes the practical limitations of the material. SK&A worked closely with the project architect, general contractor and CFS suppliers to locate and size the bearing walls in a way that allowed the building to function as intended and achieve the required economy of construction. The heaviest load-bearing walls use box studs made of (2) 600S350-97 studs at 24" o.c.
Building height restrictions in the District of Columbia place a premium on limiting the floor-to-floor height and thus, the structural depth of the floor. The ability of the CFS studs to support a thin floor system without the need for steel beams was instrumental in providing 9'-0" ceilings in residential units. The CFS stud-bearing walls were able to be located within each unit as well as at demising walls to limit the floor span and, consequently, the floor depth.
Using CFS stud walls and flat strap bracing allowed for an increased pace of construction. Shear wall end members were comprised of boxed CFS studs with some lower-level posts transitioning to tube steel. Thru-floor hold down rods were used for continuity between floors. The maximum flat strap bracing used is a 4"x 54 mil strap applied to both sides of the shear wall.
CFS studs were also used for the elevator shaft and stair tower walls, allowing all vertical elements above the podium to be provided by the CFS suppliers. Special detailing was required at the perimeter of stairs and elevator walls to maintain the necessary two-hour fire rating. SK&A devised a concrete "ring beam" that would trace the perimeter of the shafts and match the depth of the floor system (5 1/2").The southeast tower includes a penthouse amenity space that could not be framed with bearing walls. Structural steel posts were used above the roof to support steel beams framing the penthouse. To avoid continuing these posts all the way down to the podium, the post locations were closely coordinated to align with the bearing walls below. Stud packs were located within the bearing walls to support the penthouse posts and limit the need for structural steel shapes.
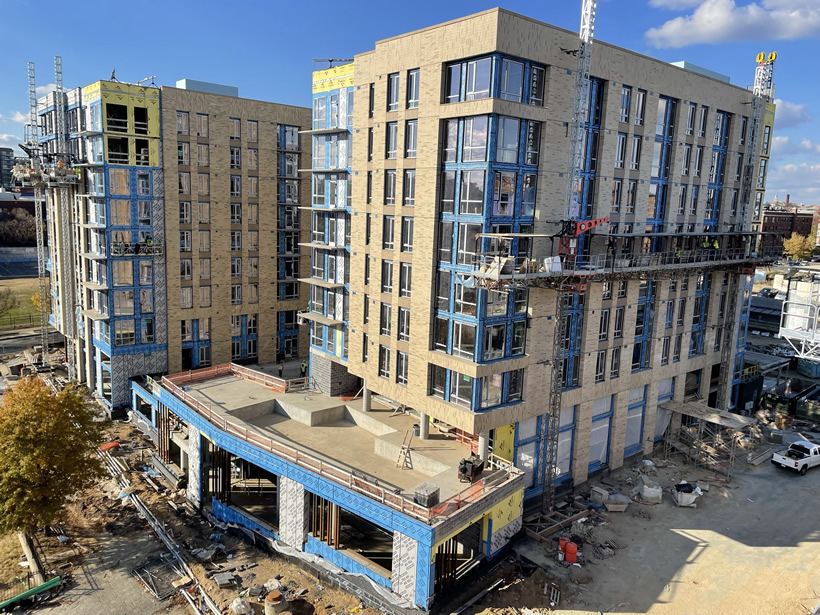
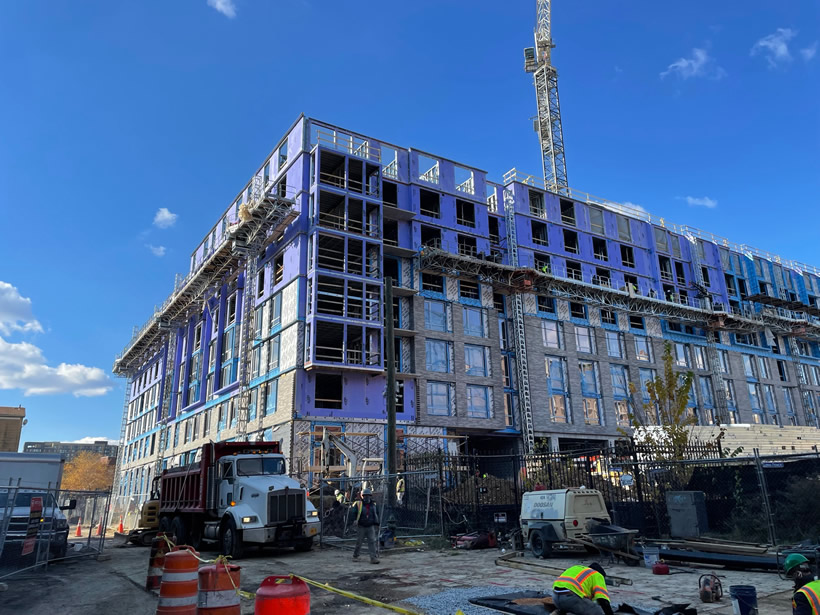
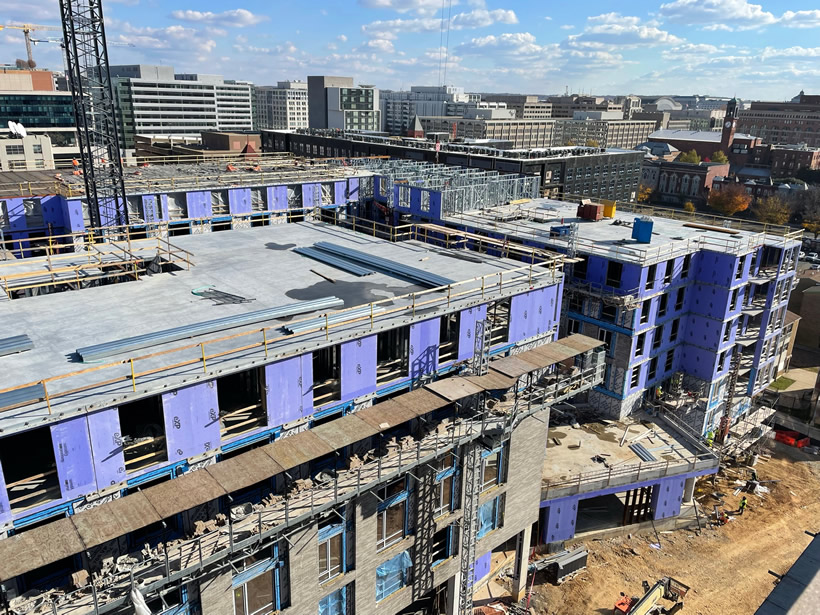
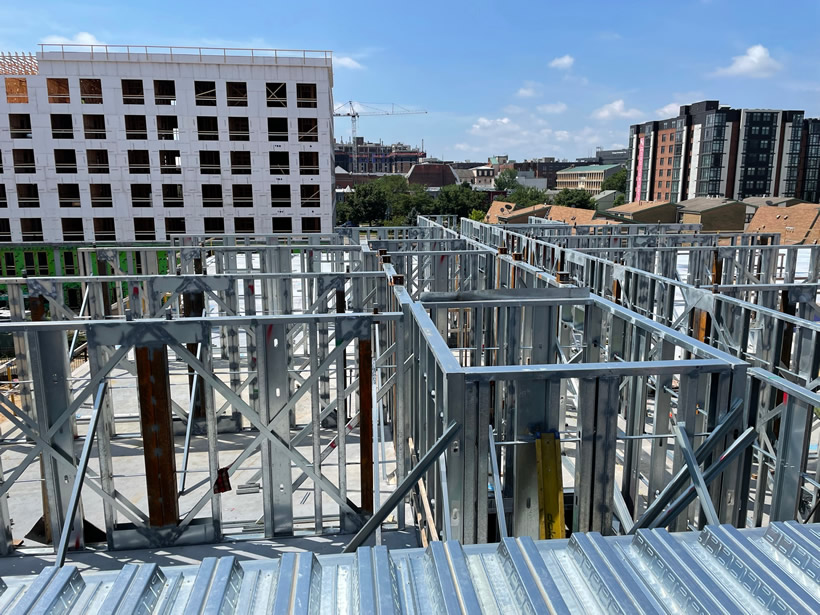
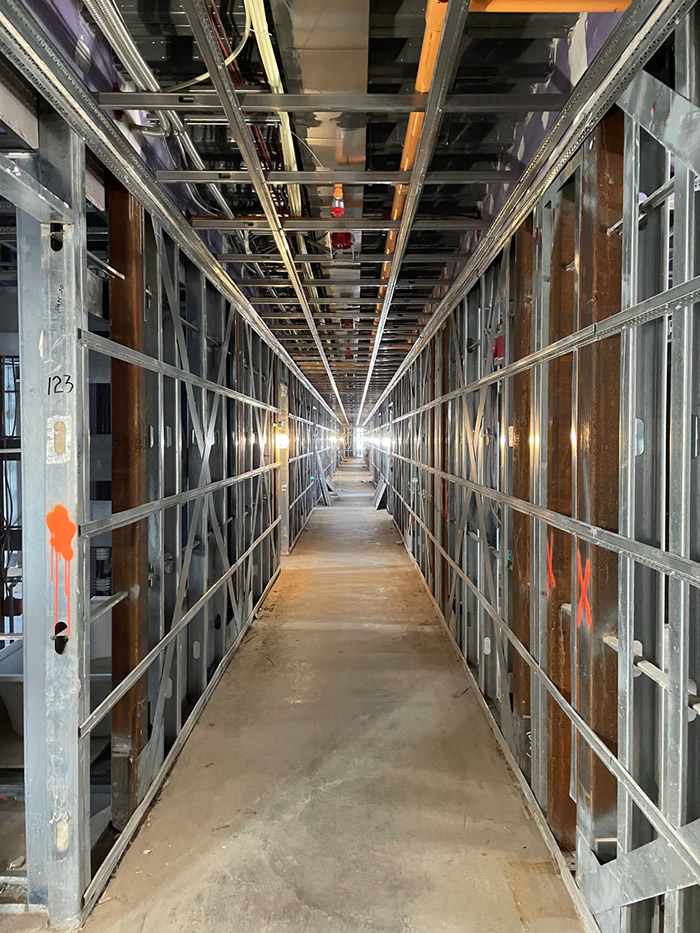 |
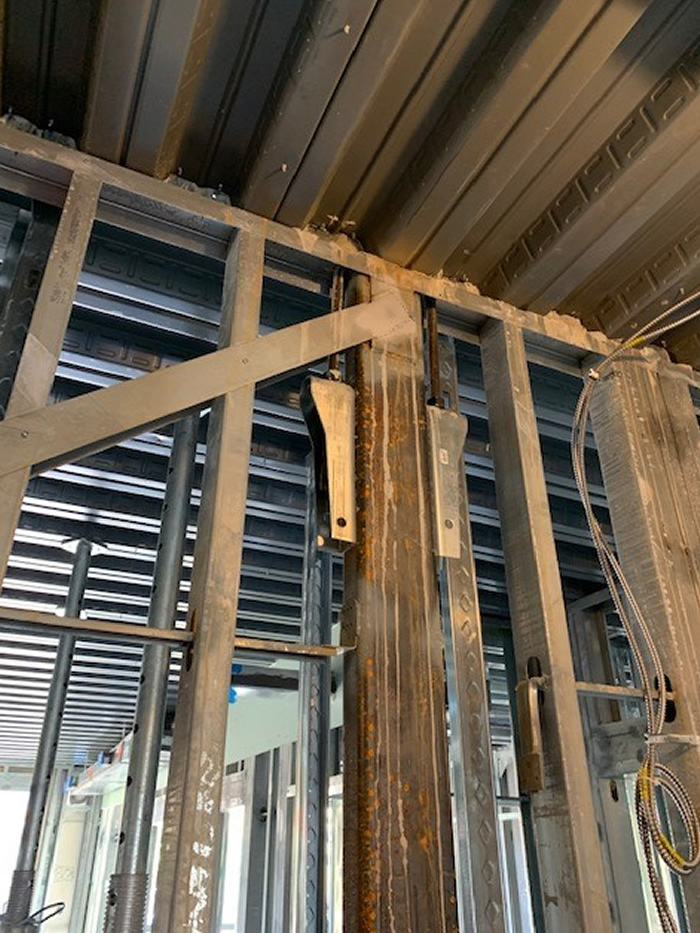 |
Photos courtesy of SK&A Structural Engineers
|
|
|