2022 CFSEI CREATIVE DETAIL AWARD WINNER
SECOND PLACE
McCLURE - VIRGIN LOW RISE LAS VEGAS, NEVADA
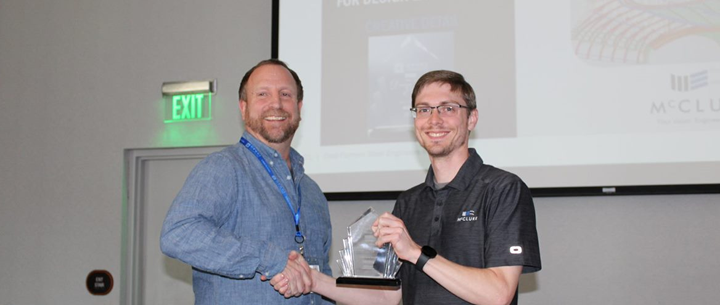
Virgin Low Rise 4455 Paradise Road Las Vegas, Nevada 89169
Completion Date: Spring 2021
Owner: JC Hospitality Architect of Record: Klai Juba Wald Architecture + Interiors Engineer of Record for Structural Work: Lochsa Engineering LLC Cold-Formed Steel Specialty Engineer: Josh Garton, P.E., McClure Cold-Formed Steel Specialty Contractor: Austin McInerny/Jason Giddy, Radius Track / KHS&S Award Entry Submitted by: Lauren Gutknecht, McClure
Project Background
Located in Las Vegas, the former Hard Rock Hotel has been transformed into a luxury Virgin hotel and casino. The McClure team provided expertise for the decorative bar inside the hotel’s casino. The primary structure is a steel-framed building with bar joists. Interior framing comprises drywall over curved metal studs, approximately 6,000 square feet of curved walls and ceiling assemblies.
Cold-formed steel (CFS) components included interior walls, openings and ceilings. Due to the ceiling weights and existing structure limitations, all roof connections were required to attach to the steel bar joists. This resulted in a secondary Unistrut ceiling framing system to create a support network.
Design Challenges and Solutions
The bar features bulbous entryway framing and a complex light shelf that follows a radiused edge (see Detail 1). The unique protrusion was created through sheet steel plates, with tabs on the edges to finish attachment surfaces. Partially through the project, the owner added curved diffusers through the curved ceiling, creating a doubly curved joint in the ceiling. To accommodate this, U-shaped trusses were arrayed along the curve and coordinated against hanger grid locations because the bar joists were expected to experience significant deflection, and framing spanned from the roof system to the foundation. An expansion joint was required between the wall framing and the ceiling. Because this would create a visible line through the finish, the architect determined the best place for this visually was after the first diffuser, meaning the diffuser had to be incorporated into the truss framing. This results in a large horizontal offset in the wall, as both sides of this assembly are finished and visible. To maintain this, the wall assembly was trussed and fixed to the foundation, adding only a horizontal thrust to the ceiling framing above—partially gravity, partially the interior pressure (see Detail 2). To keep the assembly economical, trusses were placed at 6 ft. o.c., and radiused hat channels were included to span the gaps and provide a surface for the finish.
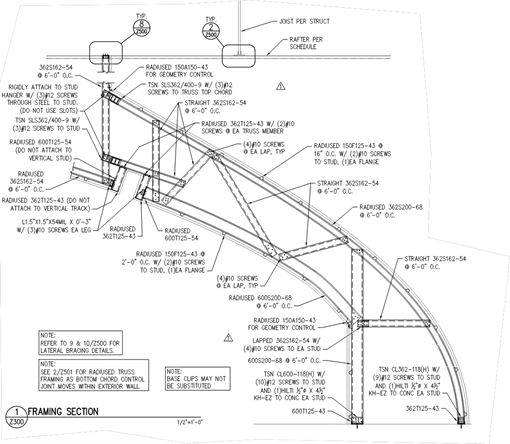
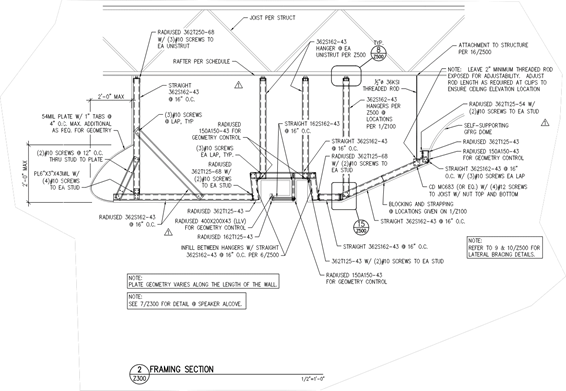
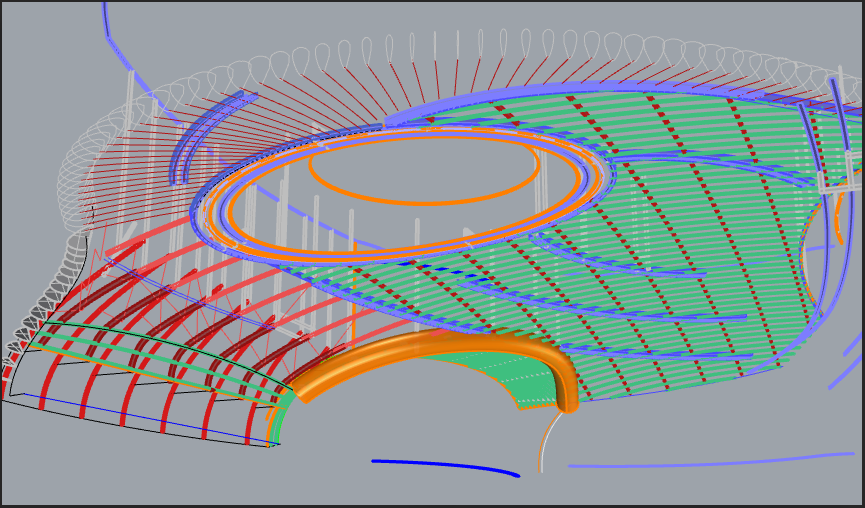
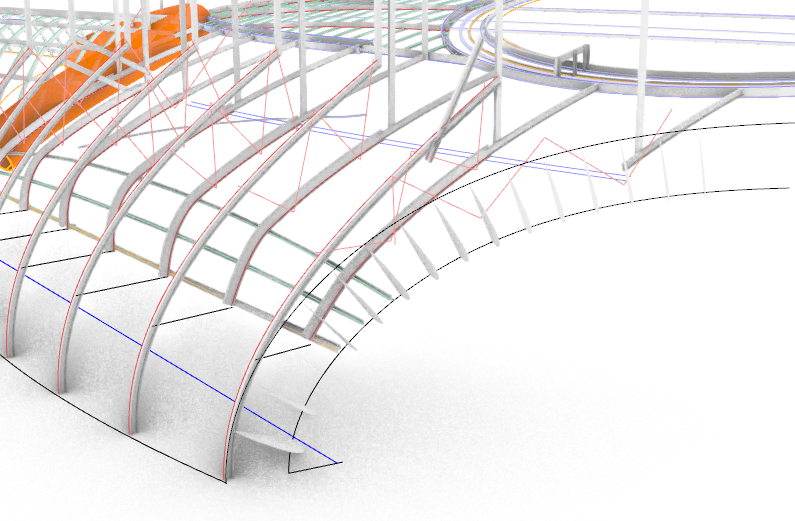
|