2022 CFSEI CREATIVE DETAIL AWARD WINNER
THIRD PLACE
THE LEFFLER GROUP - DENVER INTERNATIONAL AIRPORT GREAT HALL PROJECT, PHASE 1 DENVER, COLORADO
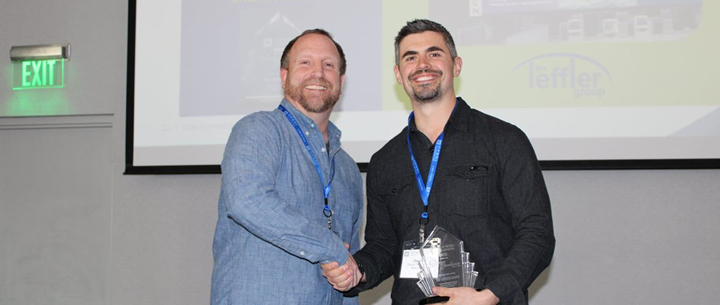
Denver Internation Airport Great Hall Project, Phase 1 8400 Pana Boulevard Denver, Colorado
Completion Date: October 27, 2021 Construction Cost: $+500 million
Owner: City of Denver Architect of Record: Joseph Crus, AIA, NCARB, Luis Vidal + Architects Engineer of Record for Structural Work: Kelly Knowles, SE, Martin/Martin Inc. Cold-Formed Steel Specialty Engineer: Ryan Nelson, P.E., The Leffler Group Cold-Formed Steel Specialty Contractor: Breck Dane, Four Star Drywall Award Entry Submitted by: Ryan Nelson, P.E., The Leffler Group
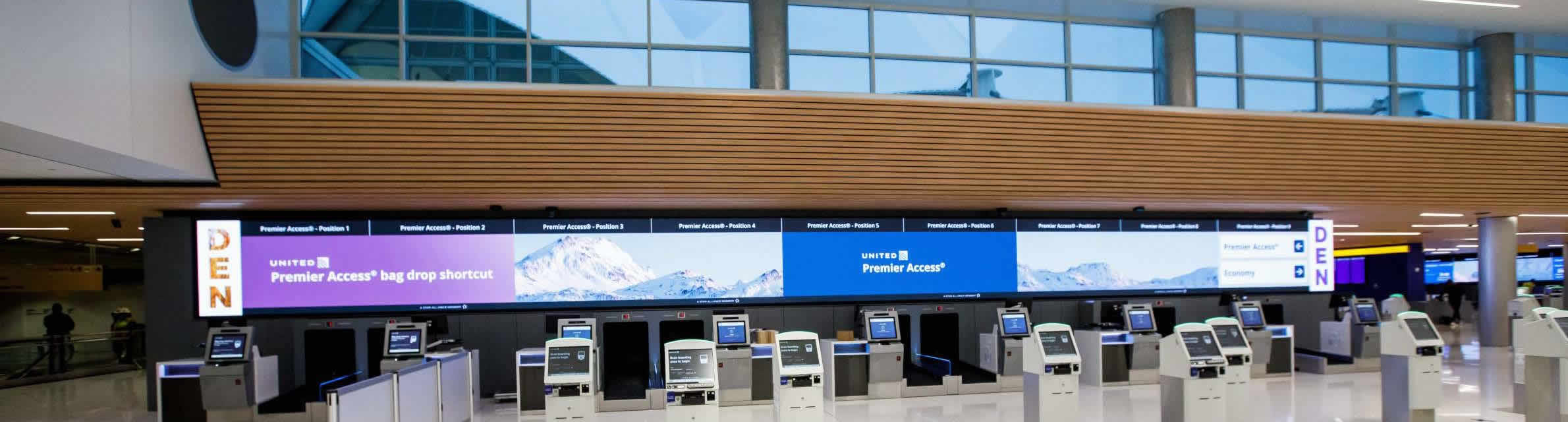
Project Background
The Denver International Airport (DIA) Great Hall Project has a large soffit detail used throughout the Level 6 check in areas. The architectural design required integrating large ductwork, a continuous linear diffuser, cable trays, fire sprinklers and decorative wood framing. Below the soffit framing, wall framing occurred at the new baggage check-in locations that needed custom openings and large digital display supports that also needed to be braced by the soffit framing.
Design Challenges and Solutions
Initial challenges included dealing with the differential movement between the wall framing on the floor below and the soffits framing from the roof structure and interstitial floor framing above. An initial solution was to try to get the wall and soffit supported from the floor; however, there was not enough space between the baggage handling equipment and MEP to build a robust cold-formed steel (CFS) structure to support everything. We then looked at fixing the soffit structure to the roof framing and interstitial floor steel. We came up with CFS framing that could be installed at 4’-0" on center that would allow for the large ductwork to pass through and provide consistent support for the decorative wood soffit element. Next, we looked at how to support the wall framing below. We determined that a vertical movement joint could be hidden in the light cove segment of the wall framing. The proposed vertical movement joint worked well to achieve the seamless look, the necessary movement and structural integrity.
We then explored different connection types for the soffit mounting. New challenges arose as the City of Denver initially prevented the use of powder-actuated fasteners (PAFs) and limited the contractor's use of gas-actuated fasteners due to security concerns about fastening activity sounding like gunshots. Since the gas-actuated fasteners have much lower capacity in steel, we succeeded in obtaining an exception from the City of Denver to use PAFs in the soffit detail to reduce the welding requirements where possible. This helped the contractor to speed up the time of construction.
Our design team also worked closely with the GHP Virtual Design Collaboration group to skillfully coordinate the details with all other trades, limiting field issues and construction conflicts.
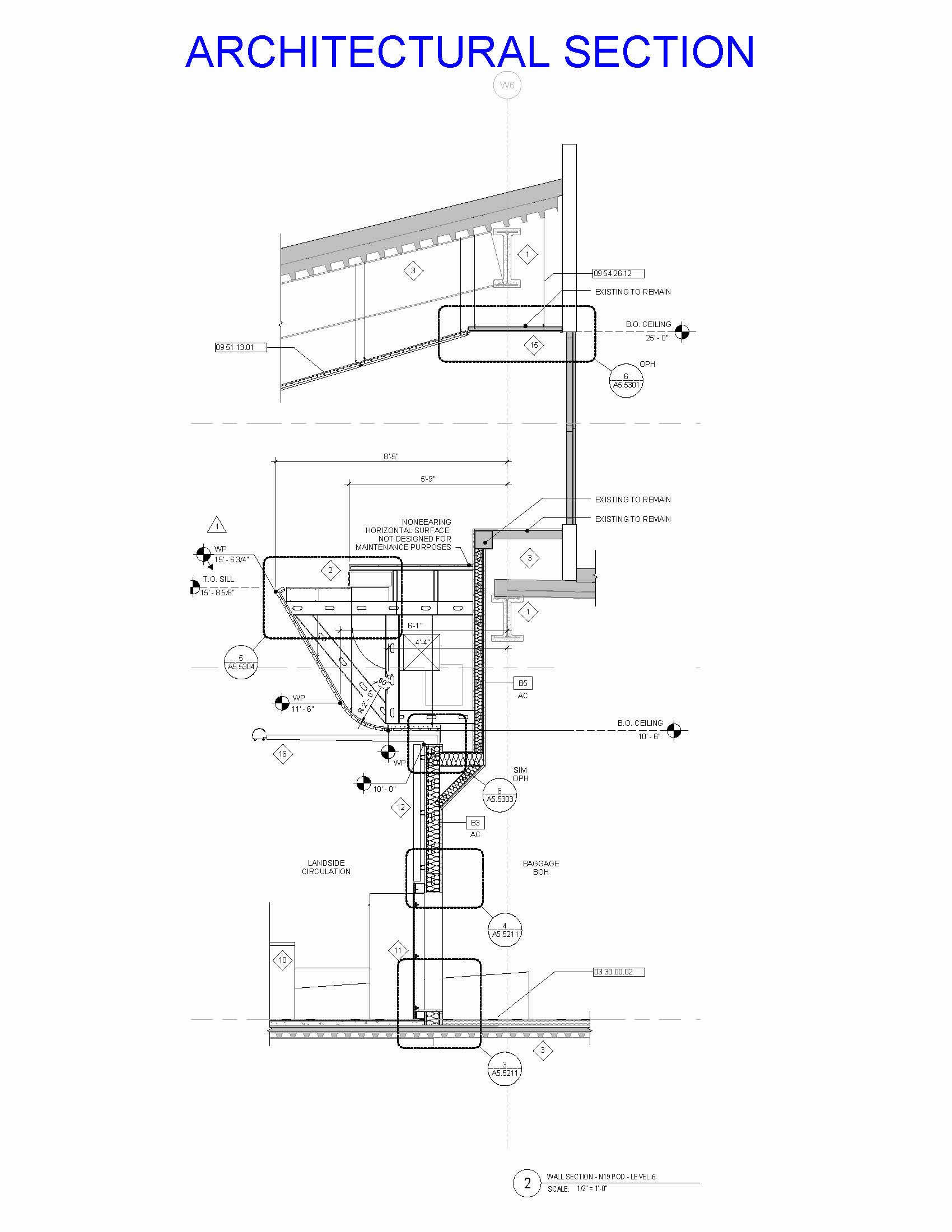
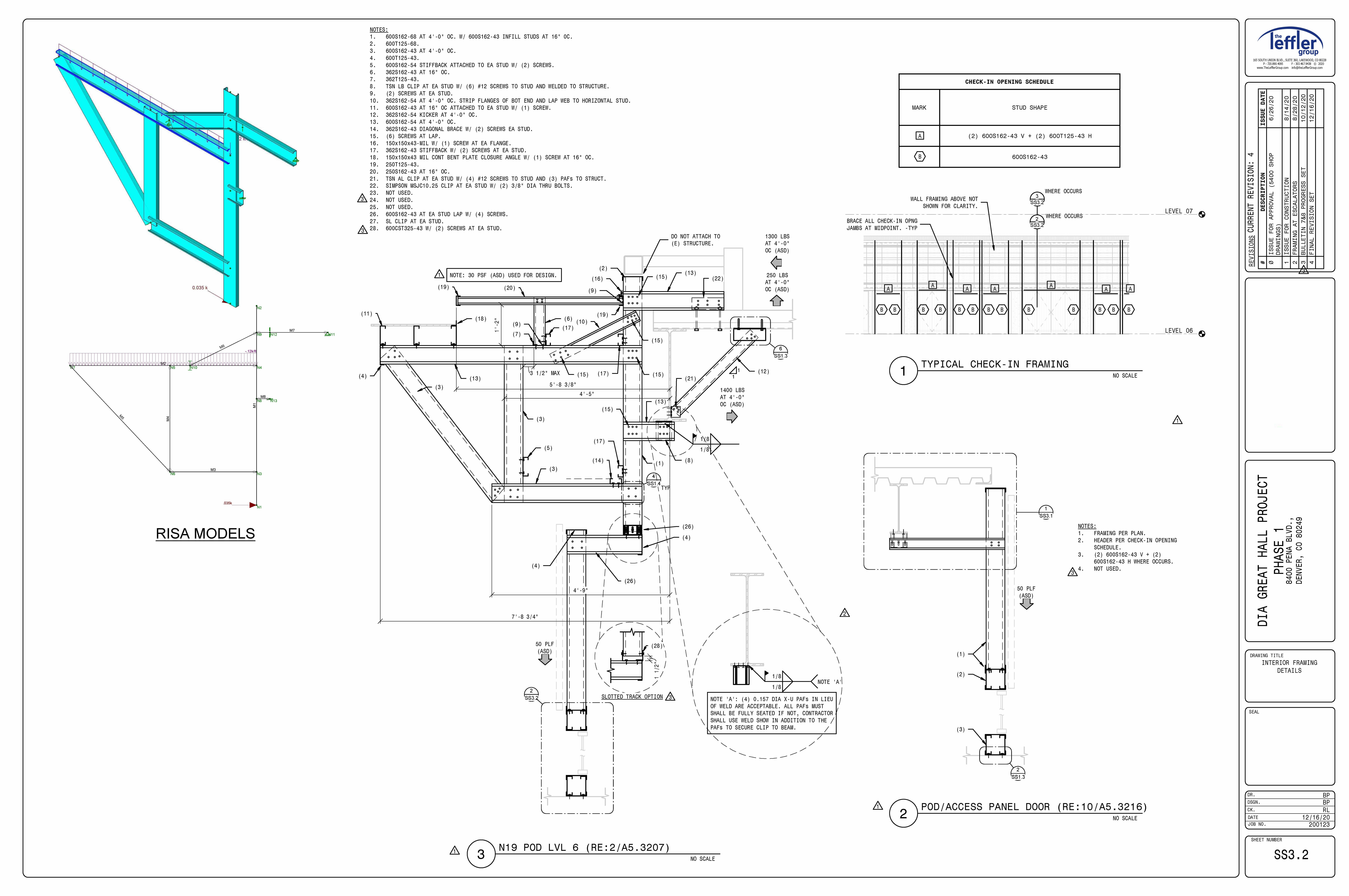
|