2023 CFSEI DESIGN EXCELLENCE AWARD WINNERS
SECOND PLACE - MUNICIPAL/SERVICES
DIGITAL BUILDING COMPONENTS – MAYO WEST TOWER PHOENIX, ARIZONA
Mayo West Tower 5777 E. May Boulevard Phoenix, AZ 85054
Completion Date: December 2022/Dry In) Completion Date: $41 Million
Owner: Mayo Clinic Architect of Record: Ray Smith, HKS, Inc. Engineer of Record for Structural Work: Christa Chau, PK Associates Cold-Formed Steel Specialty Engineer: Tony Polusny, P.E., Pangolin Structural and Casey Quackenbush, Pangolin Structural Cold-Formed Steel Specialty Contractor: Travis McCoy, P.E., S.E., LEEP AP, Digital Building Components and Venkata Charan, P.E., Digital Building Components Award Entry Submitted by: Venkata Charan, P.E., Digital Building Components
Project Background
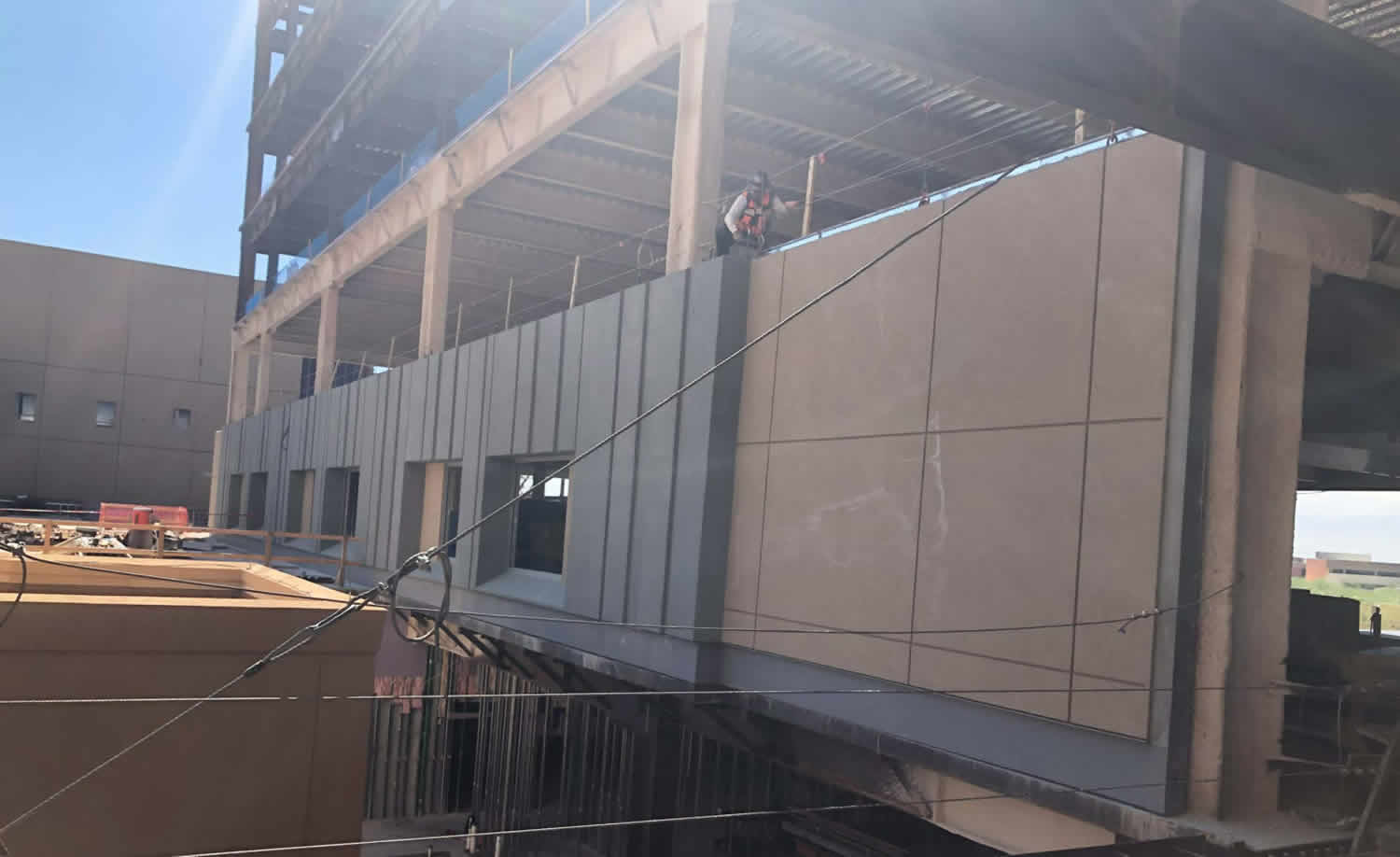
Mayo West Tower is a seven-story structure (concourse plus six floors above grade) with approximately 140,000 square feet of prefinished exterior cold-formed steel (CFS) non-load bearing wall panels. The building addition will focus on expanding clinical programs including the Emergency Department, Laboratory Medicine, Intensive Care and Medical-Surgical Beds, Observation Beds, Apheresis, Ambulatory Infusion Center, Dialysis, and Radiology, and will increase capacity of the existing hospital. The building structure comprises concrete over metal deck with steel moment frames and prefinished exterior CFS non-load bearing wall panels encompassing the structure.
Digital Building Components (DBC), based in Phoenix, is the Cold-Formed Steel Fabricator and Pangolin Structural is the CFS Specialty Engineer for the project. DBC fabricated around 1,500 wall panels prefinished with windows preinstalled. The sizes of the panels are around 24' in length, 15' in height, and 24" thick.
Design Challenges and Solutions
The size of CFS wall panels is around 24" thick x 24' long x 15' height.
The unique aspect that sets Mayo Tower apart from all other exterior projects is the panel size. The walls are 24" thick with 6" EIFS placed over 6" J girts that are placed over 12" studs. During inception of the project, DBC’s design team looked at different ideas to fabricate a 24"-thick wall that is 24' long prefinished with windows preinstalled. They decided to use 12" studs as the first layer wall and then place the 6" J girts horizontally, which act as bracing for these long panels during shipping and hoisting.
Transition from 24"-thick wall to 12"-thick wall within the same panel
The team realized there was an issue with transitioning from a 24"-thick wall to a 6"-wall for hoisting. The architect did not want a panel joint separating them, so Digital Building Components and Pangolin Structural devised the solution of fabricating them as separate panels and connecting with welds to hold the panel in place for lifting as one single piece.
Transition of 24"-thick walls to 4" thick around openings
Another challenge involved the transition from a 24"-thick wall panel to a 4"-thick wall occurring within a window opening. DBC and Pangolin came up with the idea of extending the header within the 12" studs and adding 2-1/2" studs as infill studs to make up that transition. This enabled us to efficiently reduce the gauge of the 2-1/2" studs, saving money for the client.
Sloped sill at windows
Another unique feature about Mayo West Tower is the sloped windowsills. Digital Building Components and Pangolin were designed to keep the traditional windowsills with a 12" track and tweaked the design by adding an angled bent plate with 2-1/2" studs to make up the sloped sills.
Panels with "L" shaped and "Z" shaped corners
Several panels in the project are not simple rectangular wall panels. Instead, they are "L" shaped and "Z" shaped around the corners. For example, one of the walls is around 30' long and is only 6' wide and has an "L" shaped corner that is extending 3' out from the main panel. DBC and Pangolin came up with the idea of creating boxed studs at the end and using CFS straps as "X" bracing to increase the stiffness of the connection between the main panel and sub panel. The most difficult part with these "L" panels is they need to be connected to a thin strip of slab that is only 12" wide and extends 7' from the main building. The DBC and Pangolin solution was to bypass these panels by two floors and stack them together so that installation of the panels was less difficult.
Designing panels at parapet for future expansion and lifting them with a panel splice in-between.
Designing walls at parapet was another unique aspect of this project. The parapet walls needed a panel splice within the main wall to account for future vertical expansion of the hospital. We designed the parapet to be stitched with screws to the lower panel for future removal.
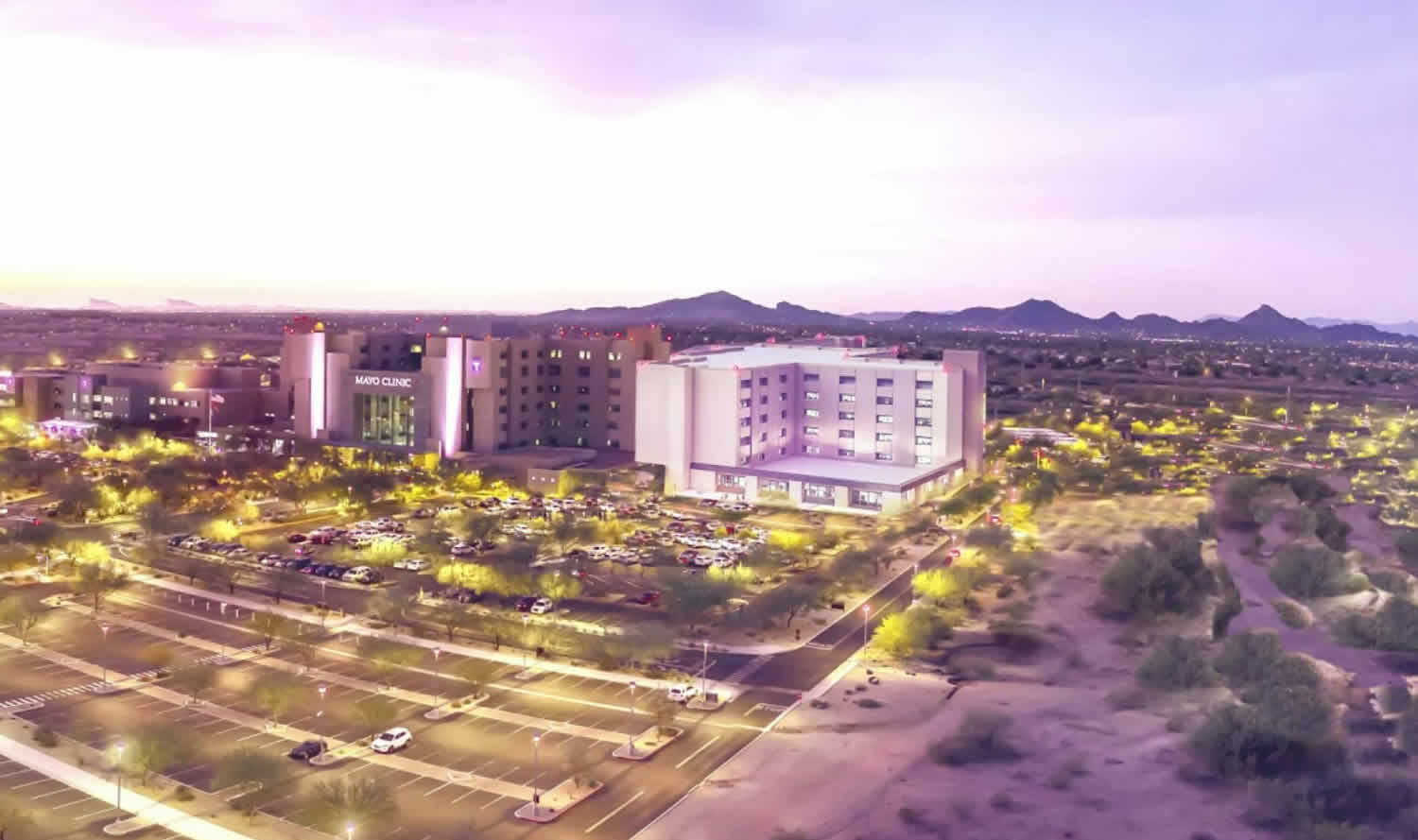
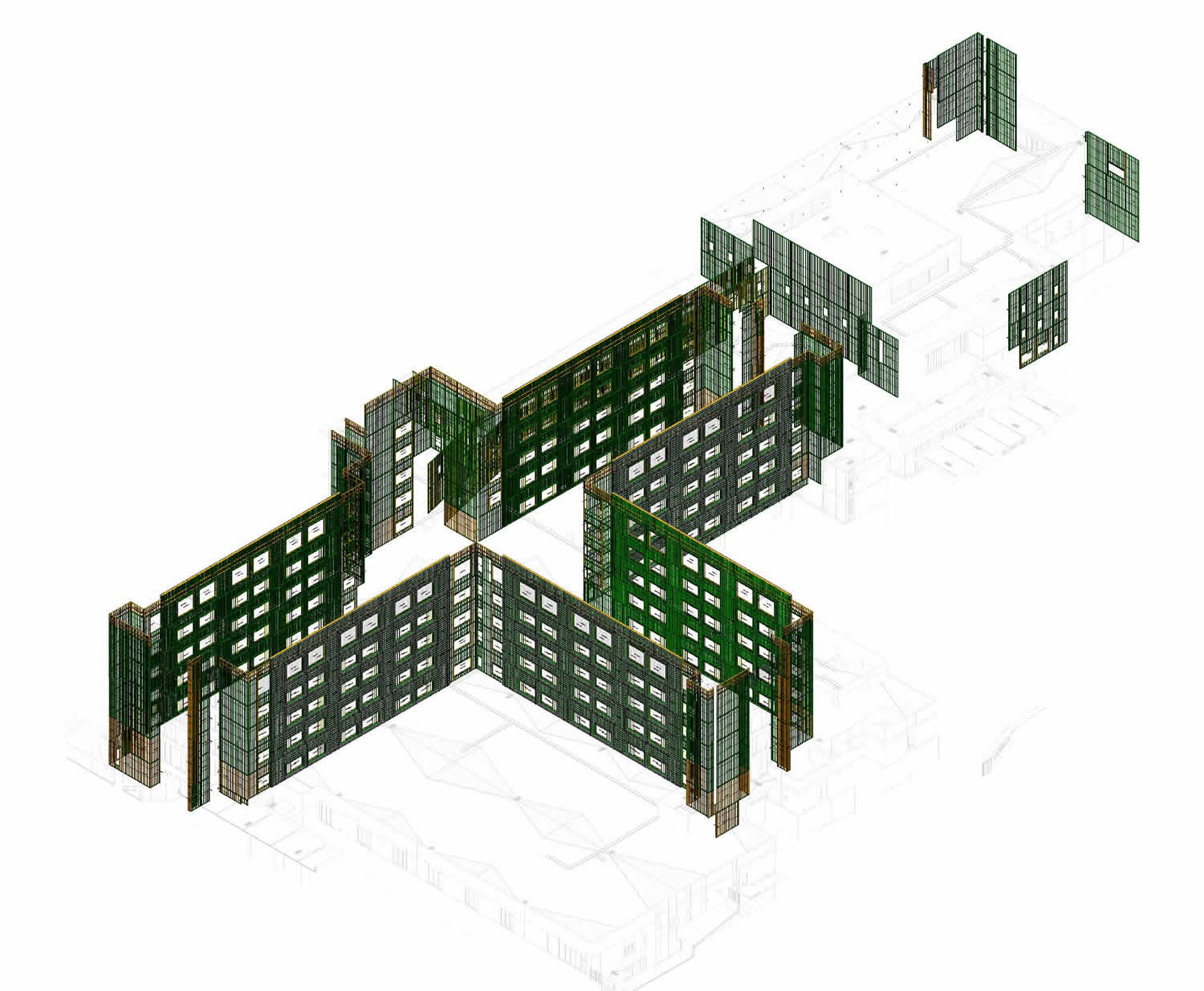
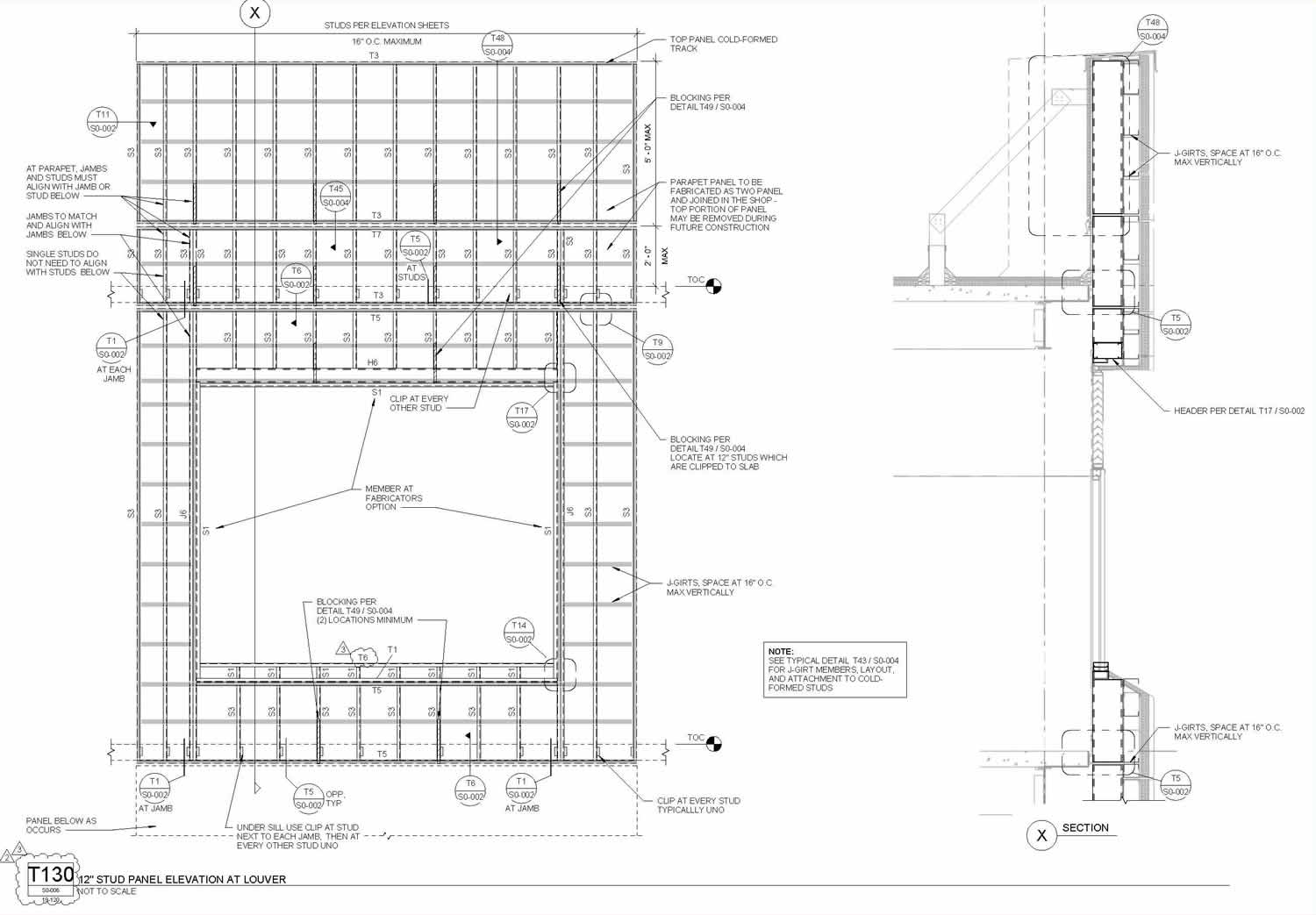
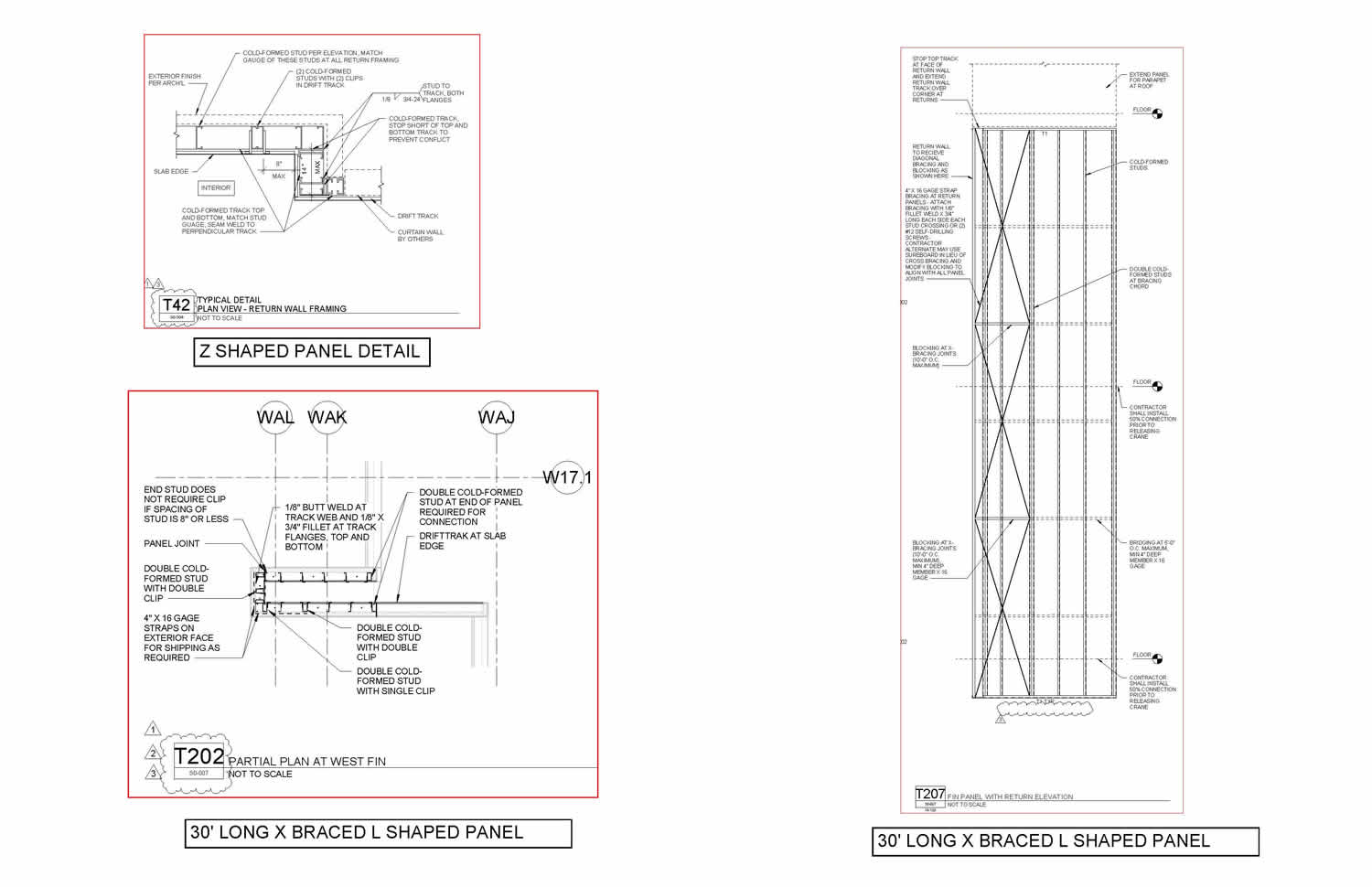
|