2023 CFSEI DESIGN EXCELLENCE AWARD WINNERS
FIRST PLACE - MUNICIPAL/SPORTS
MARTIN/MARTIN, INC. – PENNSYLVANIA STATE UNIVERSITY LASCH BUILDING RENOVATION STATE COLLEGE, PENNSYLVANIA
Pennsylvania State University Lasch Building Renovation 201 Hastings Road State College, PA 16801
Completion Date: September 2022 Completion Date: $48 Million
Owner: Pennsylvania State University Architect of Record: Todd Carll, HOK Engineer of Record for Structural Work: Mary E. Haynes, Stahl Sheaffer Engineering, LLC Cold-Formed Steel Specialty Engineer: Shane Ewing, Martin/Martin, Inc. Cold-Formed Steel Specialty Contractor: Paul Broderick, BLUvera LLC Award Entry Submitted by: Grant Doherty, Martin/Martin, Inc.
Project Background
The Pennsylvania State University (Penn State) recently completed an 89,000-square-foot addition to the Lasch Football Building. The addition is adjacent to the indoor and outdoor practice facilities and includes a 13,000-square-foot weight room, massive locker room, athletic training facilities, whirlpool therapy, meeting rooms, video production suite, coaches and staff offices, a well-appointed players' lounge, and the academic support center and computer room.
The Lasch Football Building is named after (Louis and Mildred Lasch) who have been instrumental in fundraising for the football program since 1959.
The structure includes both one- and two-story steel-framed sections and features a large expanse of a glass curtain wall for visual access to the practice field and interior lighting within the facility.
Design Challenges and Solutions
Martin/Martin was contracted by BLUvera and the general contractor, Mortenson Construction, early in the design process to help guide the exterior wall framing scheme through design and detailing efforts. The design-assist process was extensive and complicated, involving complex architectural design elements on the building facade.
The exterior wall panels and cladding framing elements were modeled and prefabricated. Complete coordination was critical to ensure successful incorporation of these elements with the supporting structural steel. The steel fabricator did not initially model the structural steel. When a model was provided, it was not at an adequate level of development to support accurate design coordination. In support of the client and design team, Martin/Martin supplemented this modeling effort, resulting in minimal field installation conflicts and issues.
Working closely with the client, Martin/Martin optimized wall panels and assemblies to maximize the work that was performed in the factory and minimize on-site installation requirements.
Some of the most complex and interesting design features included:
West End Picture Frame
The wall bump-out elements at the head, sill, and sides of the large curtain wall on the west end of the building became known as the “picture frame.”
The picture frame was comprised of six different cold-formed steel (CFS) assemblies that were factory-completed and shipped to the jobsite. The jamb assemblies were full height, and the head and sill were split up into two pieces, for shipping and installation. Careful coordination was required to ensure that these assemblies could be shipped to the site with sheathing and air/vapor barriers (AVB), and that connections would be made at discrete points to the structural steel framing.
The jamb assemblies were returned top and bottom to allow the more complicated framing and waterproofing miter at the corner to occur in the factory. This fabrication design detail resulted in a simpler vertical joint in the field. Unlike typical wall framing elements, these three-dimensional assemblies could not be analyzed in traditional CFS design software. They were modeled in SAP2000, the design forces were extracted, and members were evaluated using CFS 13.
Canopy Framing
When Martin/Martin was first engaged on the project, the practice field side (north) first-floor cantilever canopies were framed in structural steel and would have been either field-framed or heavy shop fabricated assemblies. Supporting the client, Martin/Martin’s engineers were able to redesign the canopies, converting them to relatively lightweight shop-fabricated CFS assemblies, reducing the structural steel to single-wide flange outriggers at approximately 30-foot spacing increments. The series of canopy sections included a nine-foot-long cantilever portion, fully framed with CFS.
The architect wanted recessed, hidden gutters and roof drains, which was originally accomplished by notching and reinforcing heavy, wide flange beams. By altering the framing to span parallel to the gutters, Martin/Martin easily framed around the gutters without notching the framing.
These assemblies were shipped in one piece, with sheathing and AVB, and simply dropped between the structural steel outriggers.
Exterior Wall Panels
Inclusive of the exterior framing, wall framing was fully modeled and panelized in a factory. In addition to framing, Martin/Martin also modeled the sheathing and GreenGirts, which were also installed in the factory, saving valuable field labor and eliminating the need to scaffold the building exterior.
Preinstalling the sheathing, fluid applied air and vapor barrier, GreenGirts, and insulation provided challenges in handling, stacking, and shipping the panels. Martin/Martin provided engineering support for these stages of construction to ensure panels were not damaged during shipping, handling, and installation.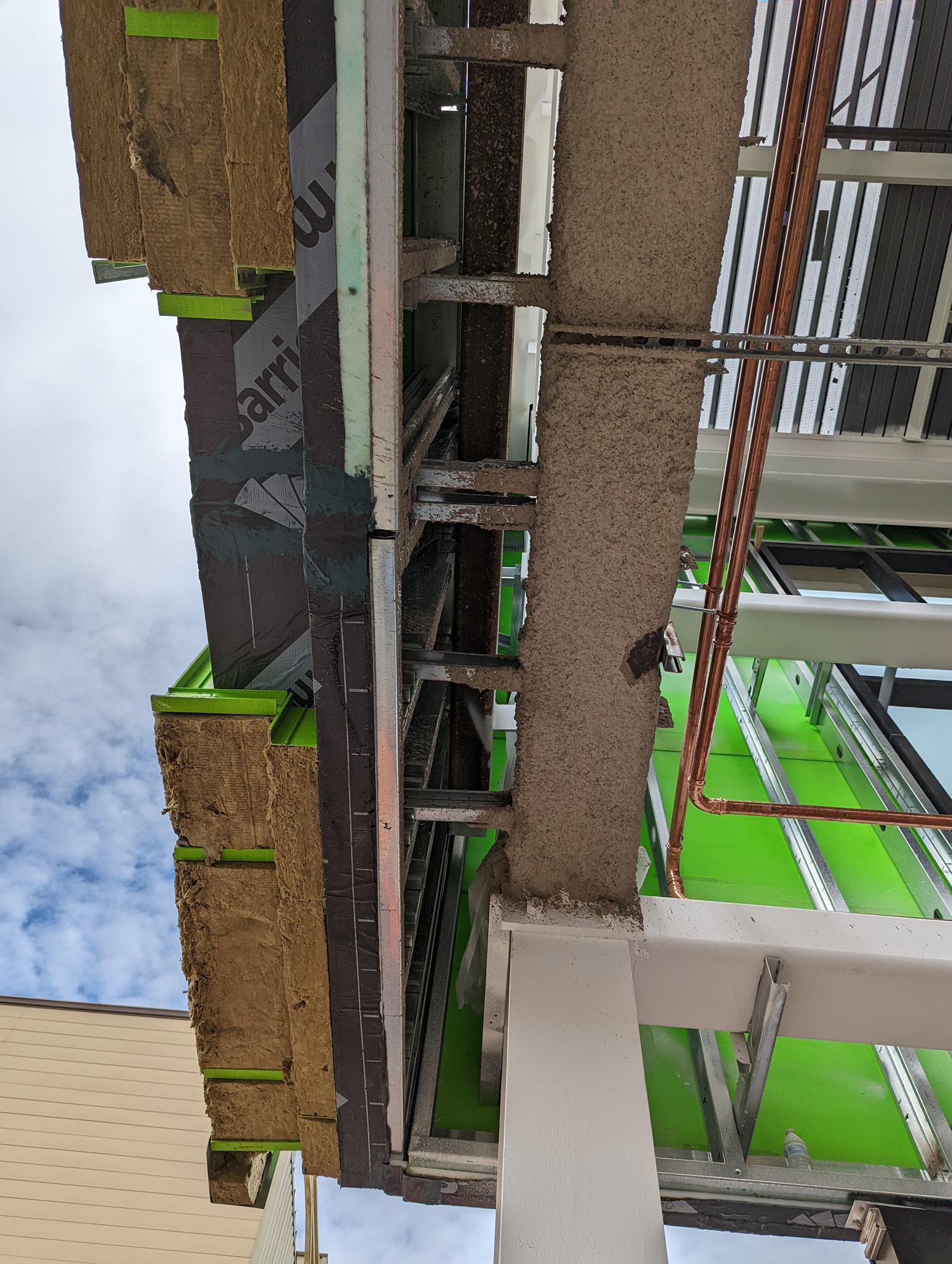
Everyone involved in this successfully completed project pushed the boundaries of prefabrication. The careful BIM coordination between Martin/Martin, the design team, and other trade partners resulted in field installation with minimal problems and minimal site-installed elements. The result is a modern, open addition to Penn State’s impressive athletic complex.
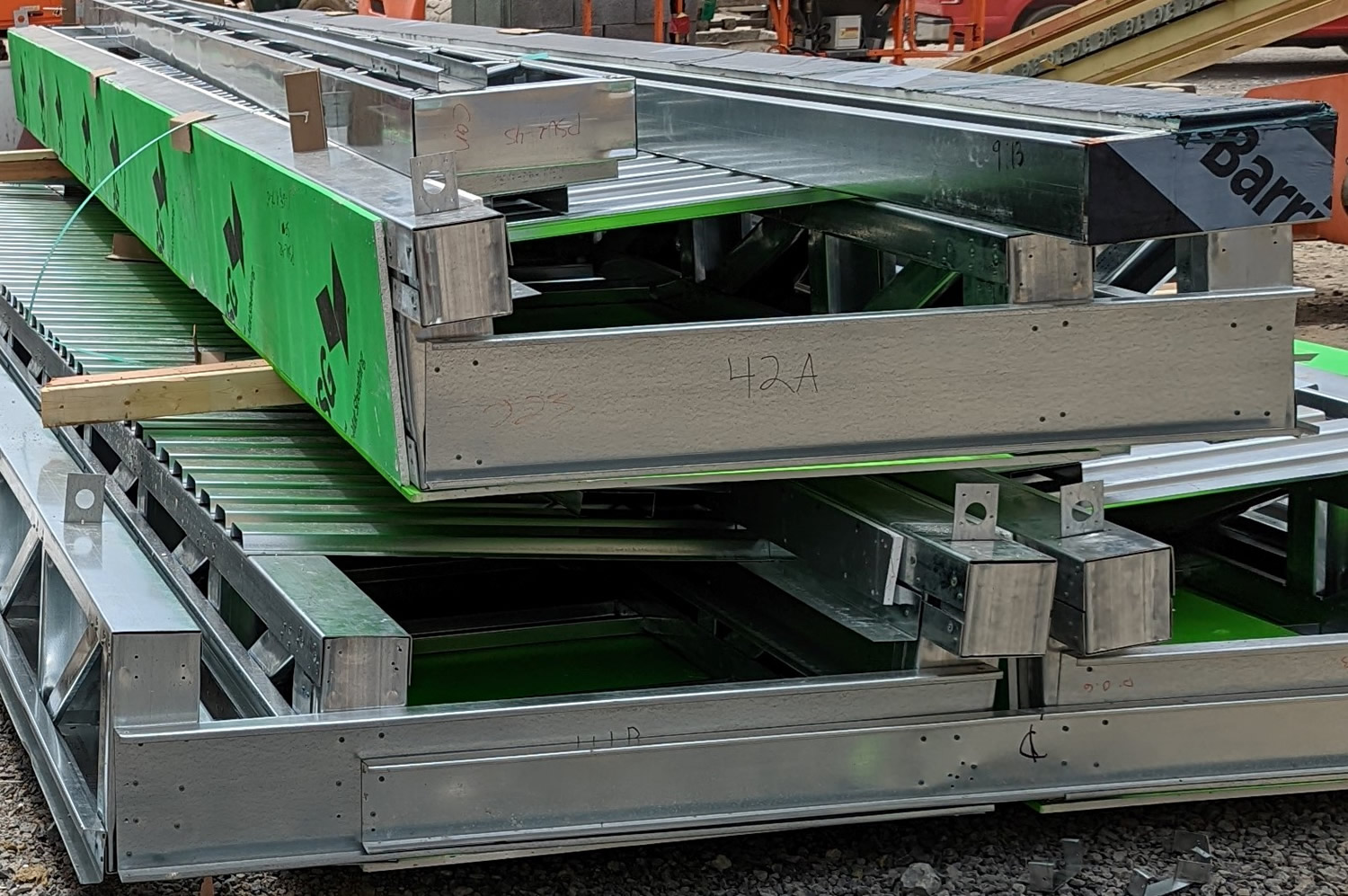
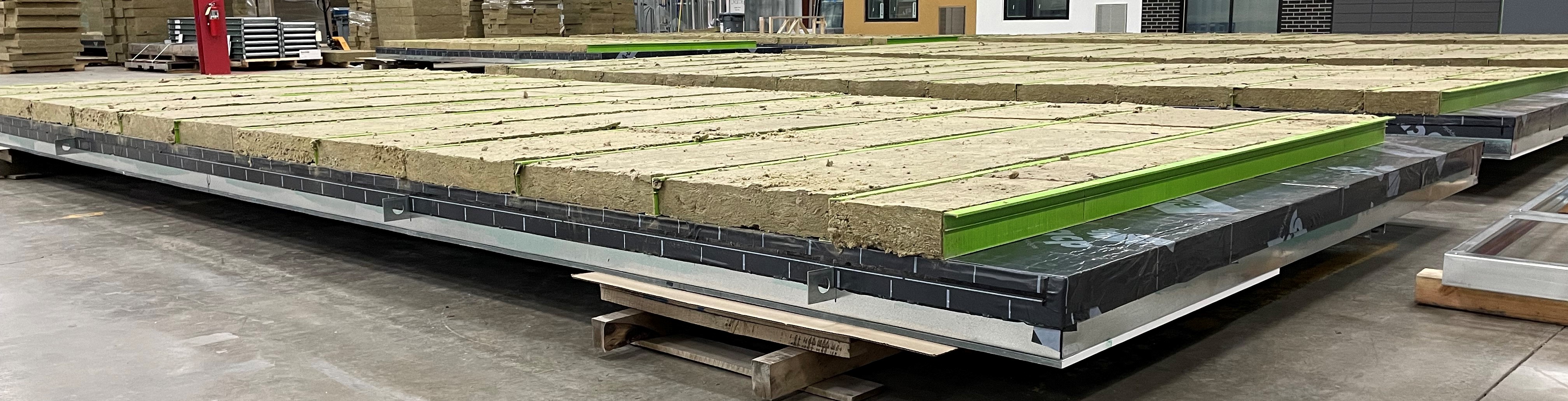
|