2020 CFSEI DESIGN EXCELLENCE AWARD WINNER
FIRST PLACE – COMMERCIAL
raSmith – STEW LEONARD’S – PARAMUS, NEW JERSEY
Stew Leonard’s 700 Paramus Park Paramus, New Jersey 07652
Completed: September 2019
Owner: Stew Leonard’s. Architect of Record: The Sullivan Architectural Group. Engineer of Record for Structural Work: TEC Engineering, LLC. Cold-Formed Steel Specialty Engineer: raSmith, DGC Capital Contracting Corp. Cold-Formed Steel Specialty Contractor: Doug Congdon, Duraframe Steel Framing Solution. Award Entry Submitted by: Derek Putz, P.E., raSmith and Kyle Poquette, raSmith
Project Background
In September 2019, Stew Leonard’s brought their signature brand of supermarket and liquor store to Paramus, New Jersey. While the grocery store chain has operated stores along the eastern seaboard since 1969, this site marks its first venture into New Jersey. Stew Leonard’s is famous for offering farm-fresh produce from local sources and includes singing and dancing animatronic displays amongst its various kiosks and shelves.
The Stew Leonard’s Paramus location is actually the site of a former Sears department store in the Paramus Park Mall. While raSmith was not part of the 80,000-square-foot store’s redevelopment design team, it was contracted to provide structural analysis and design for two exterior architectural features that are trademarks of Stew Leonard’s across the New England area: silos.
These silos are an important part of the brand’s image as a farm-fresh food store. While the new store’s two silos are purely decorative and will not actually be utilized for food storage, they do feature a heavy-duty design of curved cold-formed shear walls that are wrapped in two layers of plywood and finished with stucco. Both a small and a large silo were designed, with the small silo consisting of two approximately 7-foot-tall segments, and the large silo with three 16-foot-tall segments. The larger silo, after completion, stands at roughly 50 feet tall.
Design Challenges and Solutions
Duraframe, the panelizer responsible for supplying the prefabricated cold-formed steel framing, brought raSmith into the project to utilize their cold-formed steel expertise. Plans called for a large, freestanding silo to be placed behind the store, with a smaller one on the front canopy near the entrance. raSmith designed the structure to consist of three cylindrical segments, with each segment consisting of six curved X-braced shear wall panels. These panels would be erected in the field so that they would form a perfect 16-foot-tall cylinder, with each segment being stacked on the last. Two cold-formed steel-framed floors sheathed in plywood were added at the top of each segment to provide support against out-of-plane wind loading. The end result is a 50-foot-tall silo that consists of six stacks of three shear wall panels.
The steel structure’s freestanding design was self-sufficient, with each stacked shear wall being independently anchored to the concrete foundation below, and with each shear wall being braced by the adjacent shear wall. Out-of-plane wind forces were braced by a circular cold-formed steel and plywood floor installed at the top of each segment. The design, in essence, resembled a mini skyscraper—that lacked any kind of doors or windows.
Challenges arose with the anchorage to the concrete below. Given that the base track had to be segmented to make the severe curve, the base shear that typically runs along a shear wall’s base track had to be fully addressed by one or two anchors instead of the full line of PAF fasteners. The design would include enough strength for the silo to stand up against wind forces of about 20 pounds per square foot. And with the silo’s weight—almost 42,000 pounds! (or about 20 tons)—it sure needed to stand safely.
As the silo’s structure grew in height and was capped with a prefabricated dome, the exterior was sheathed in two layers of one-half-inch plywood. The second layer of plywood was added, its seams staggered with the first layer so that the silo’s stucco finish would not crack at the plywood seams.
A false hallway was also constructed to bridge the distance between the silo and the main building, although like the silo itself, this was not accessible and was purely for decoration. A second smaller silo was also designed. Similar in concept to its larger sibling, this one consisted of two 7-foot-tall segments, each consisting of four shear wall panels. The completed structure was added to the front of the store’s roof—hinting to the store’s customers that farm-fresh goods awaited inside.
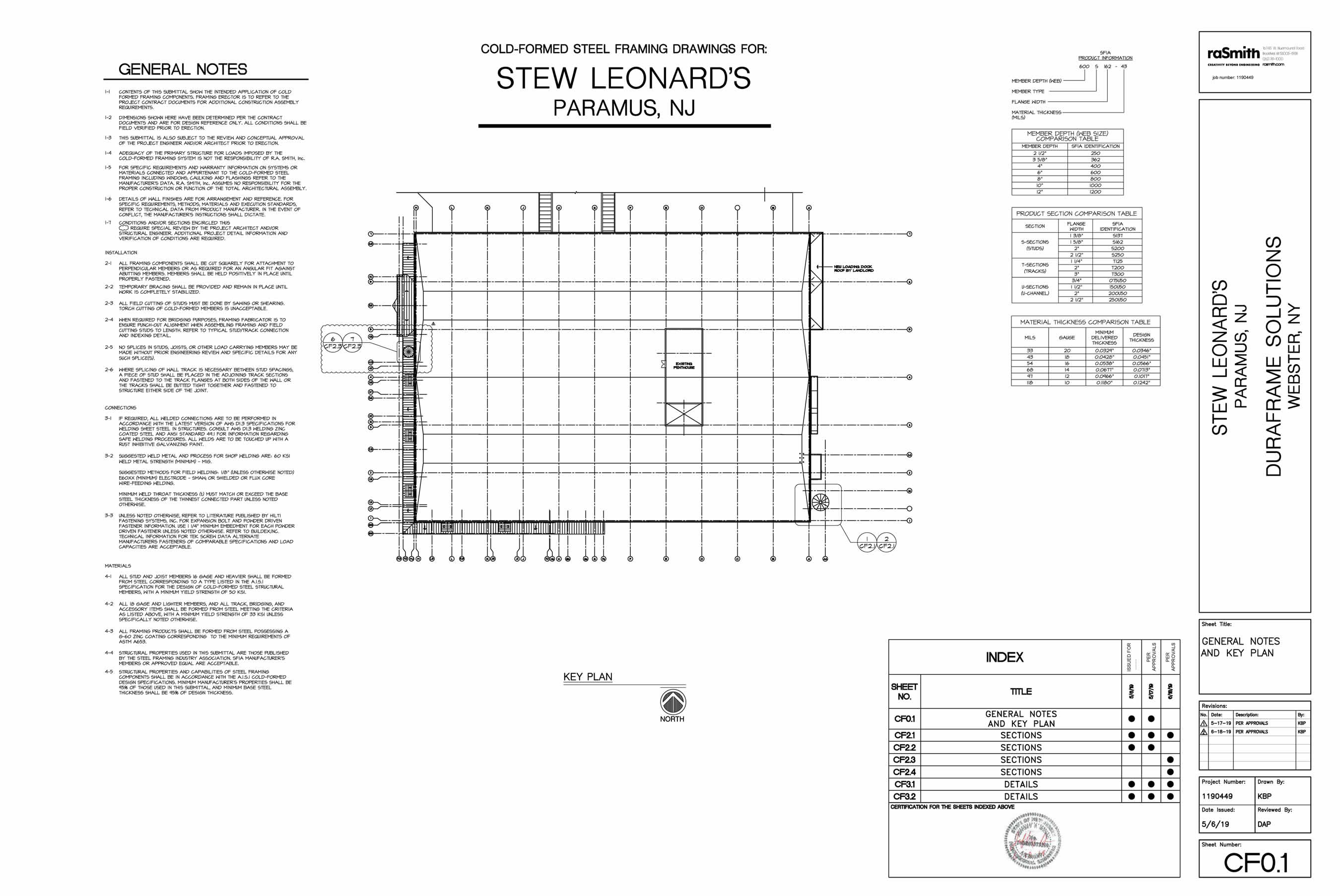
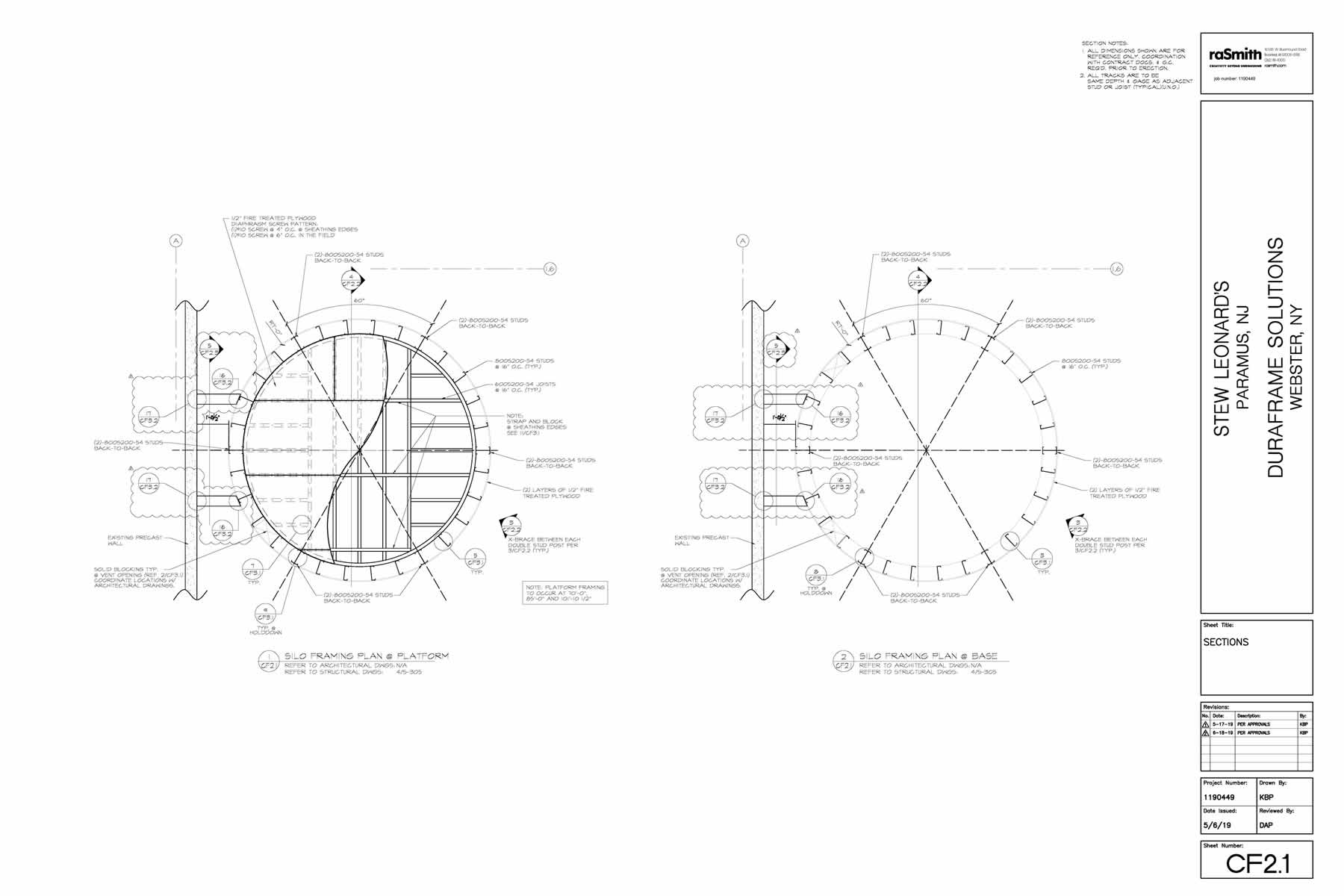
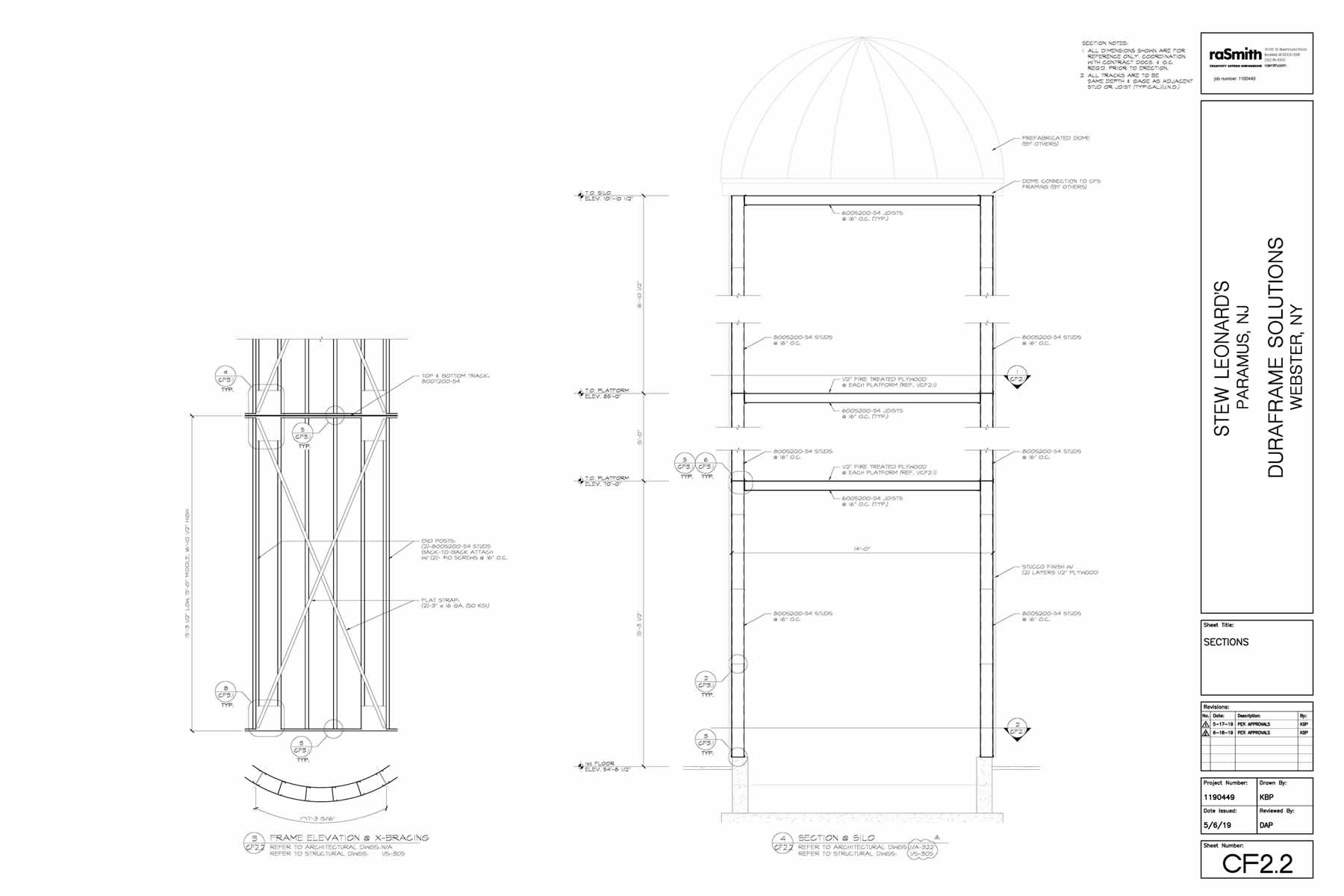
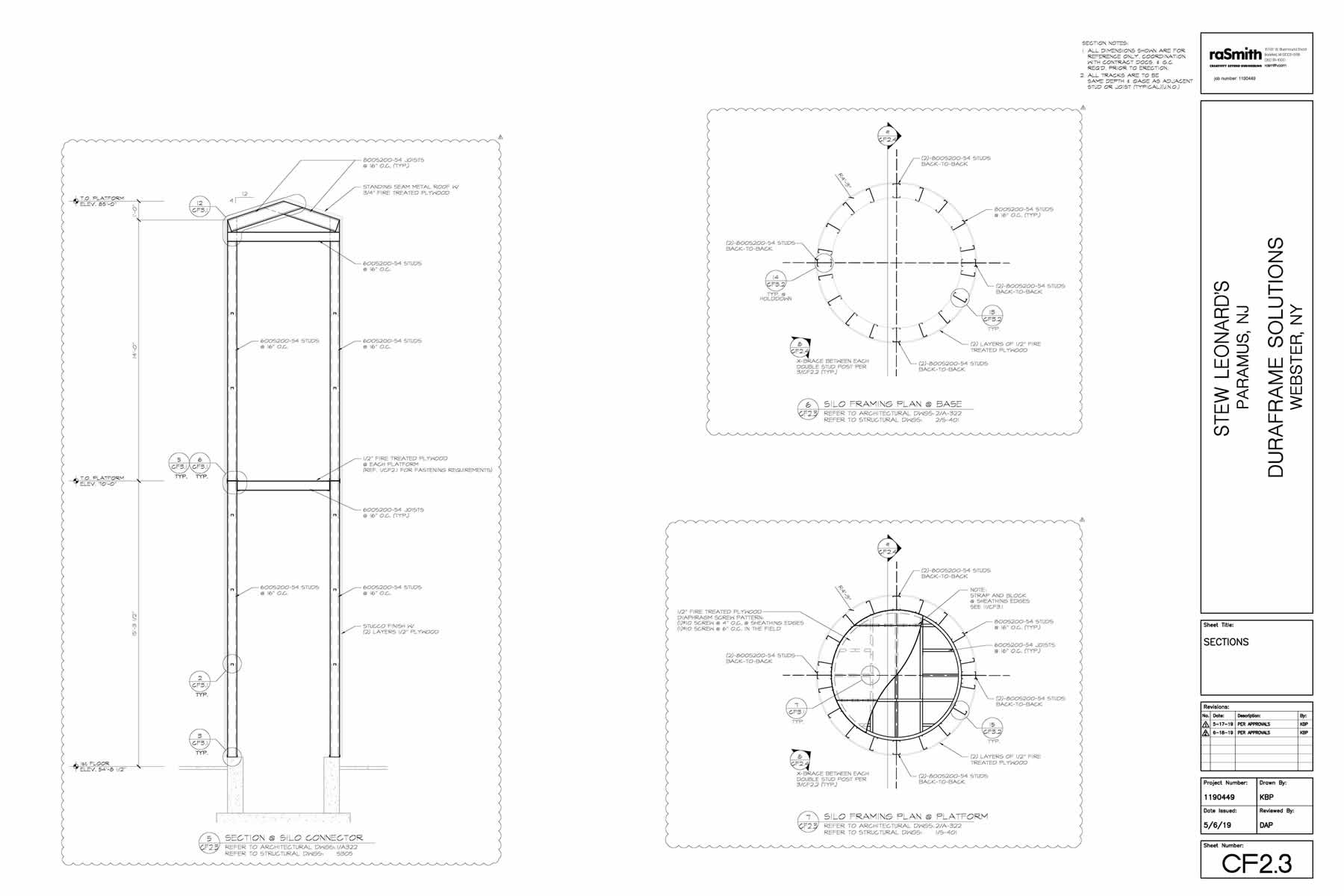
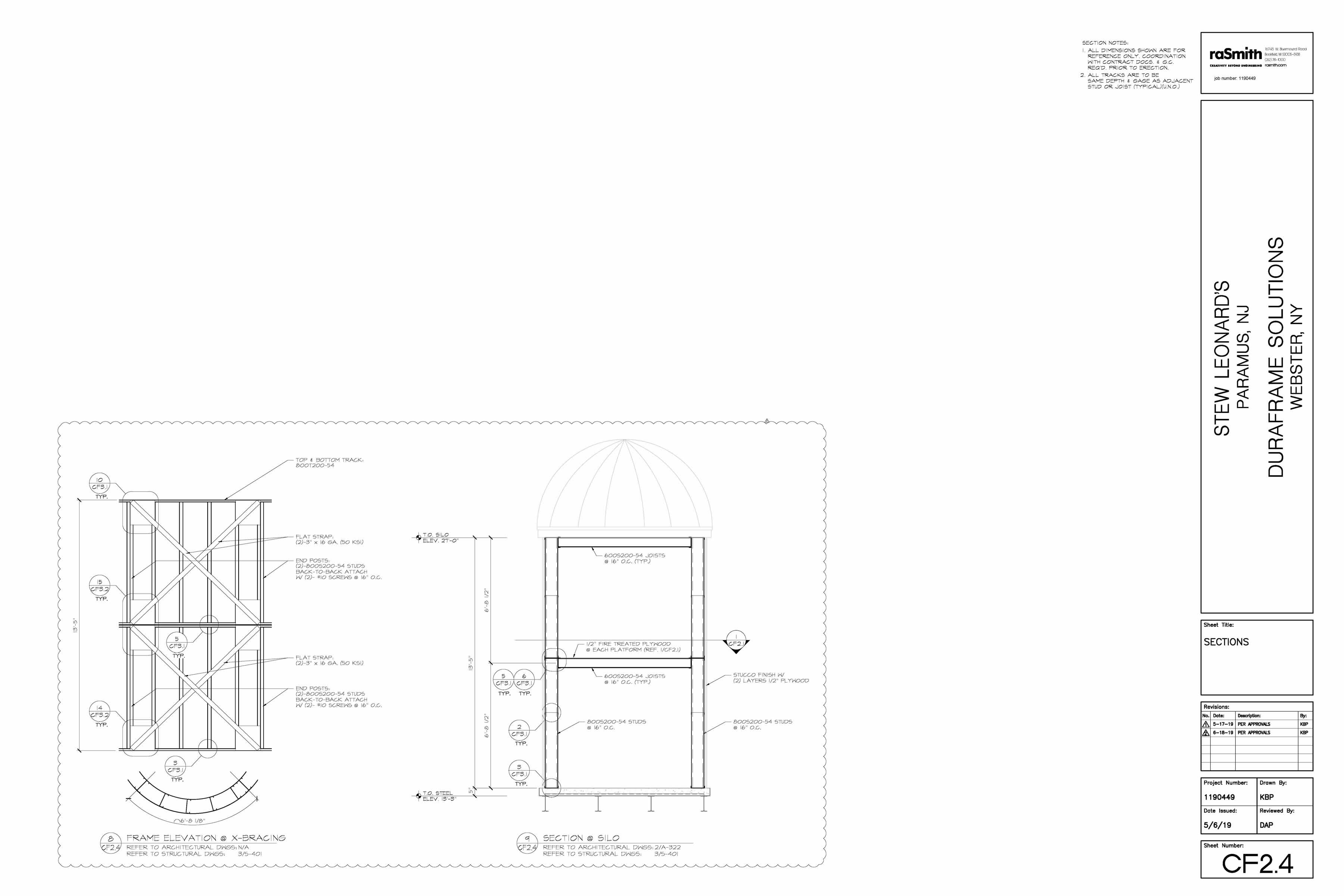
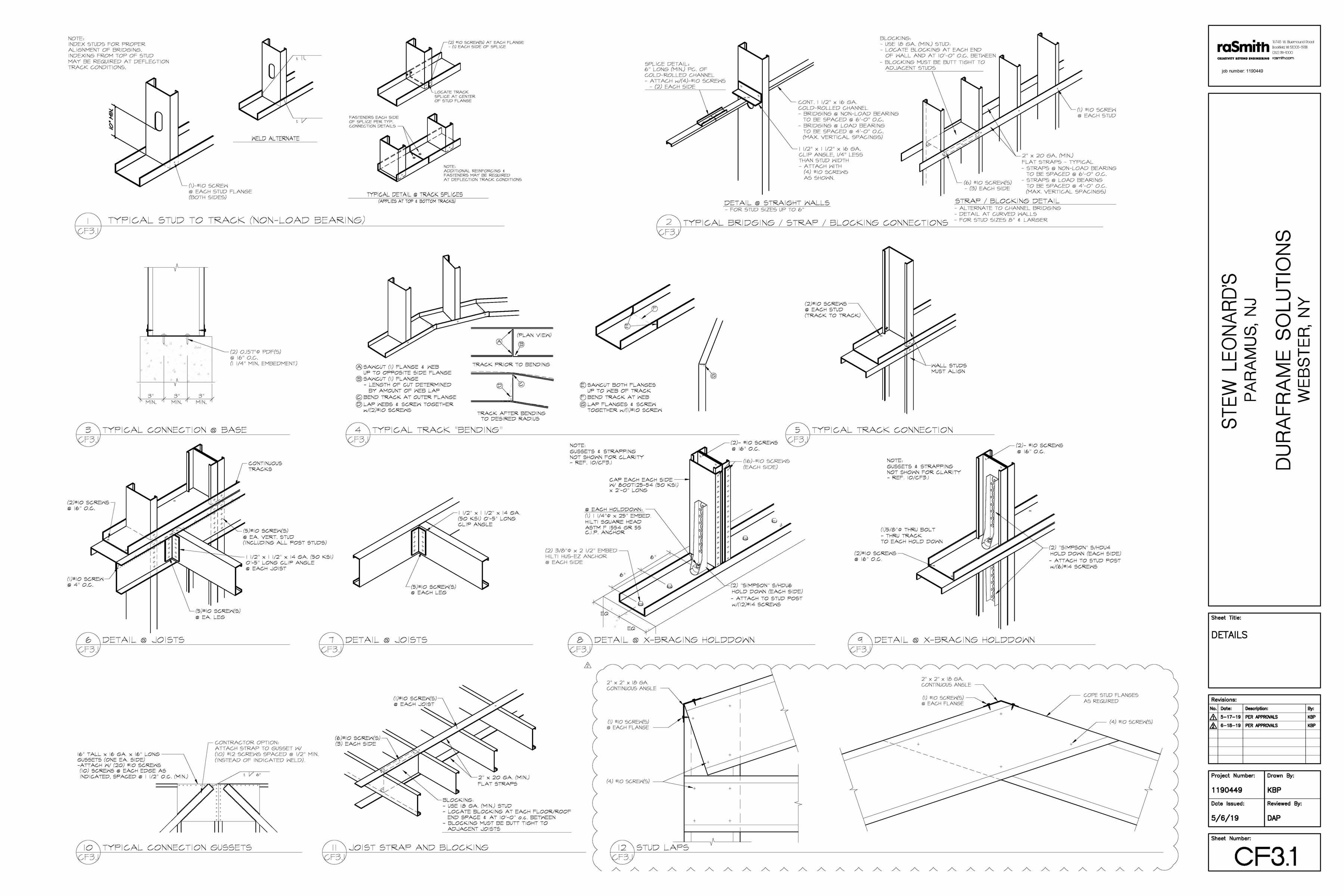
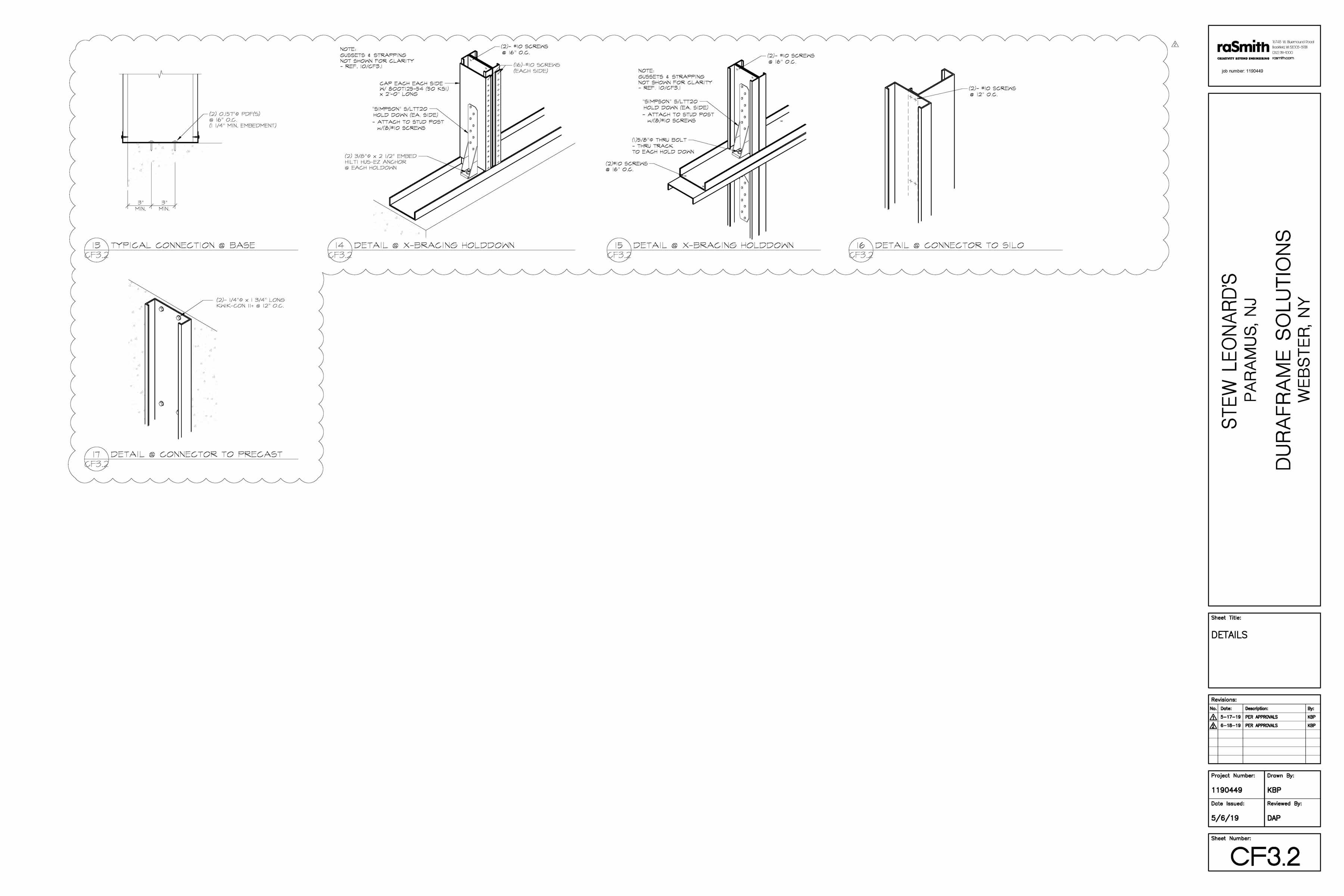
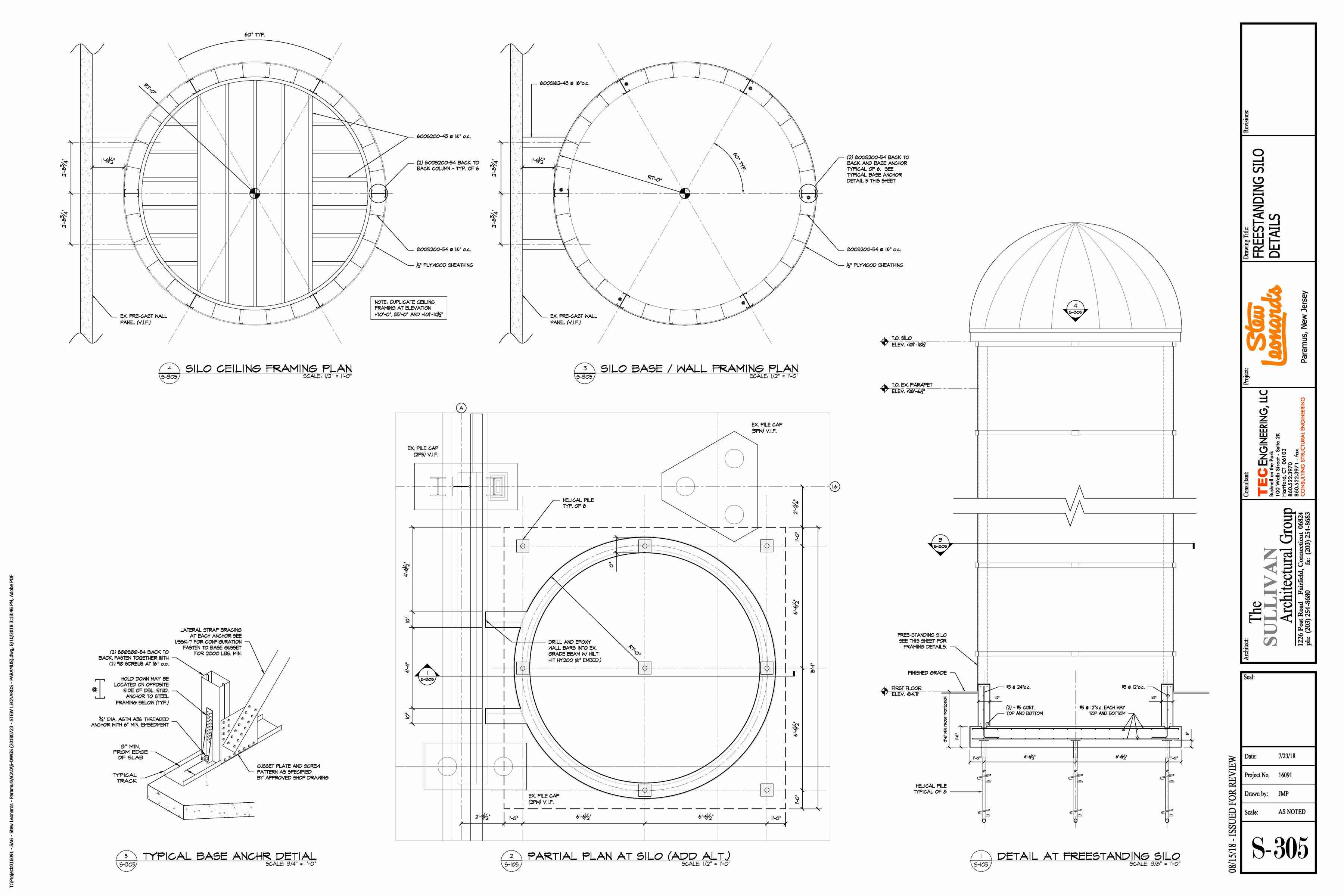
|