2023 CFSEI DESIGN EXCELLENCE AWARD WINNERS
FIRST PLACE - RESIDENTIAL/HOSPITALITY
MCCLURE – TRIANGLE SQUARE CHICAGO, ILLINOIS
Triangle Square 2115 N Elston Avenue Chicago, IL 60614
Completion Date: 2021
Owner: LMC A Lennar Company Architect of Record: Michael Hanley, AIA, LEED AP BD+C, Lamar Johnson Collaborative Engineer of Record for Structural Work: Anthony Wolanski, P.E., WSP Cold-Formed Steel Specialty Engineer: Marcus Himmelberg, P.E., McClure Cold-Formed Steel Specialty Contractor: Sean Flynn, Eisen Group, Steve Klomfar, Denk and Roche Award Entry Submitted by: Lauren Gutknecht, McClure
Project Background
Triangle Square is a 298-unit residential apartment building located in the Bucktown neighborhood, just west of downtown Chicago. The east-facing luxury apartment units have a spectacular view of the skyline from their uncovered terraces. The structure consists of six stories of cold-formed steel (CFS) framing above a single-story concrete podium. The upper levels are framed with C-stud joists spanning between demising walls with a gypcrete over metal deck floor system. The building is accented by its sloped roof structure that highlights the ingenuity required to create this complex architectural masterpiece.
Design Challenges and Solutions
As seen in Figures 1 and 2, this building has a unique geometry with nonorthogonal angles in both horizontal and vertical planes. The building layout created some difficulties and challenges during design. The thin connectors between sections of the building made it impossible to unite the structure with a single diaphragm at each level. The building was broken with control joints into five unique sections. Each one was analyzed individually for an isolated lateral system using a combination of masonry stair and elevator towers and cold-formed steel strap-braced walls. The gypcrete over metal deck floor system served as a flexible diaphragm for each separate structure. Note the creative detail design of the oversized rim track capping the floor joists used to maintain the continuous diaphragm as shown in Figure 3.
As CFS-framed buildings continue to grow taller and larger, more coordination between the engineer for the delegated CFS system and the design team is required. McClure’s role on this project was classified as a specialty engineering service, meaning McClure was involved early in the design process and helped coordinate items with the design team throughout the development of the construction documents. McClure provided loads to the podium for the engineer of record (EOR) to use in the superstructure design, helped develop details for structural steel components, and coordinated placement of columns and beams above the podium. Additionally, McClure provided the embed layout for the CFS strap-braced wall end post attachments and went as far as to provide drag strut connections to embed plates in the CMU walls for transfer of lateral forces from the diaphragms to those walls. McClure was responsible for making the structural design decisions for nearly everything above the podium level. This included services well beyond those provided by the typical delegated design professional and went further than the typical CFS delegated design would usually require. See Figures 4 and 5 which show 3D renderings of some of the non-stacking elements in the sloped ends of the building.
Within the sloped section of the building there is a single staircase that runs essentially continuously from Level 1 to Level 5 along the exterior wall of the building. Since the stairs had to align with floors while maintaining a consistent tread riser stair ratio, several of the landings did not align with any structures below. This required McClure to provide a lot of coordination for non-stacking headers and posts tracking down the building from top to bottom. This would have been very difficult to achieve without the use of 3D structural design software and BIM modeling software.
Apart from the global lateral issues created by the sloped geometry, local stability issues were also a concern. Bearing conditions as well as thrust from the sloped roof members had to be carefully considered in the detailing of the connections. See Figure 6 for the typical detail used for the sloped roof joist support condition.
The most challenging part of the project was dealing with the plan layout changes at every level caused by the sloped portion. This eliminated several strap-braced walls at the upper levels that existed below. Because the layout only provided some stacking walls all the way from the podium to the roof, several sections of the diaphragm had to be cantilevered. Additionally, some of the strap-braced walls were interrupted by openings on some floors and not others. Figure 7 shows a condition where this occurred during construction and Figure 8 shows a detail provided in the construction documents to accommodate openings at intermediate levels.
Lastly, and most important to the success of the project, McClure performed site observations and other contract administration services throughout construction. Several unforeseen issues arose during construction that required additional detailing and repairs for the contractors, and McClure‘s assistance kept the project moving. A common challenge encountered on large load bearing CFS projects immediately arose: the required podium slab edge horizontal tolerances required for CFS bearing walls were not met. The bearing walls were overhanging the supporting slab, inducing additional moment in the studs due to the eccentric support. McClure provided details to reinforce the wall studs when the concrete slab contractor failed to meet the specified tolerance in the project details. An example repair provided for this deficiency can be seen in Figure 9. Another common field error regarding layout was found on this project. Some strap-braced wall end posts did not align with an embed in the podium. Since it is very difficult to address this issue through modifications to the podium, McClure was able to provide detailing which “spanned the gap,” utilizing the existing embed and strap-braced wall end post as shown in Figure 10. An in-depth stress analysis of the components was required due to the large eccentricity between the force in the end post and the attachment to the embed plate.
The attention to detail and development of unique details for the project along with the resulting architecturally striking structure make it worthy of recognition. A lot of creativity went into making this project a success and McClure was part of the design team that made it possible. McClure’s expertise in CFS and ability to incorporate CFS and other construction materials into seamless detailing highlight what can be done with a primarily CFS structure. Triangle Square serves as a feature project for what is possible with CFS and is a beginning for more complicated architectural gems yet to be discovered. The lucky 298 tenants of Triangle Square will never recognize the technical accomplishment of the construction of this structure, but they experience the benefits of the finished space every day.
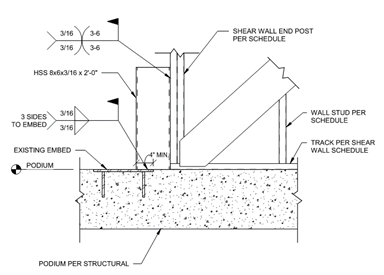
|