2020 CFSEI CREATIVE DETAIL AWARD WINNER
FIRST PLACE
THE LEFFLER GROUP – PENA HYATT PLACE – DENVER, COLORADO
Pena Hyatt Place 6110 Panasonic Way Denver, Colorado 80249
Owner: Jill West, McWhinney. Architect of Record: Jason Finnegan, AIA, GKK Works. Award Entry Submitted by: Daniel Stadig, P.E., The Leffler Group
Project Background
This detail illustrates a 10-foot-tall, 18-foot-wide, partially freestanding roof parapet wall. It utilizes a built-up cold-formed steel (CFS) girt along the back face and CFS brace anchored to a nearby concrete core wall. This wall has two depths—the South portion uses 14-inch-deep studs and continues into a five-story wing wall which protrudes from the building; the North portion has a six-inch wall bypassing the roof from the level below with a 10-foot cantilever.
This parapet wall was shown in the Contract Documents cantilevered off the roof slab edge without support, and no load path to the primary structure appeared to be specified. Early coordination from The Leffler Group requested steel support, or acceptance to use kickers at each stud along the wall into the roof diaphragm.
When performing a site visit, it was discovered that this wall did not have the requested added support, and at this stage the roof joists could not transfer the lateral reaction from the wall if kicked, nor would the roofer allow such penetrations through newly installed roofing.
Design Challenges and Solutions
The Leffler Group was called upon to propose a solution to support the 10-foot-tall roof wall while minimizing disturbance to already installed roofing, parapet cap and flashing, and exterior finishes.
Solution 1: The Leffler Group requested the Engineer of Record to provide an HSS girt across the top of the wall, one side tied back to steel eyebrow framing and the other side kicked to a nearby concrete stair core wall using a steel angle. The solution was not accepted because the steel and miscellaneous metals trade contractors had already demobilized.
Solution 2: Using an HSS girt, one end tied back to perimeter eyebrow steel and the other end supported by the CFS return wall, to be detailed as a shear wall to drag the load into the nearby concrete core. This solution was not accepted—the return wall was built and sheathed, but the shear wall anchorage and detailing were too expensive and intrusive for the already finished system.
Final Solution: Using an 18-foot-long built-up CFS girt hung from the back side of the wall with a built-up CFS brace at the wall thickness transition. The team agreed to allow a single vertical roof penetration at the brace anchorage point.
Notes:
- Since the girt had to hang from the back side of the wall, The Leffler Group created a shelf using sistered studs (RE: 7/SK16).
- North of the wall depth transition, the girt had to be tied back to the 6-inch wall (RE: 3/SK16).
- The Leffler Group aligned the girt height on the South end to allow a top and bottom clip attachment to the roof eyebrow steel (RE: 4/SK16).
- The North end of the girt had to be gravity-supported at the return wall since it was offset from the 6-inch framing (RE: 8/SK16).
- The anchorage to the core had to be installed on one side of the wall and was designed with steel due to the wall reaction into the brace and large eccentricity created for a vertical roofing penetration (RE: 6/SK16).
This fix required an entire sheet of details since every load transfer point contains different conditions. It is a great example of the versatility of cold-formed steel for meeting demanding constraints.
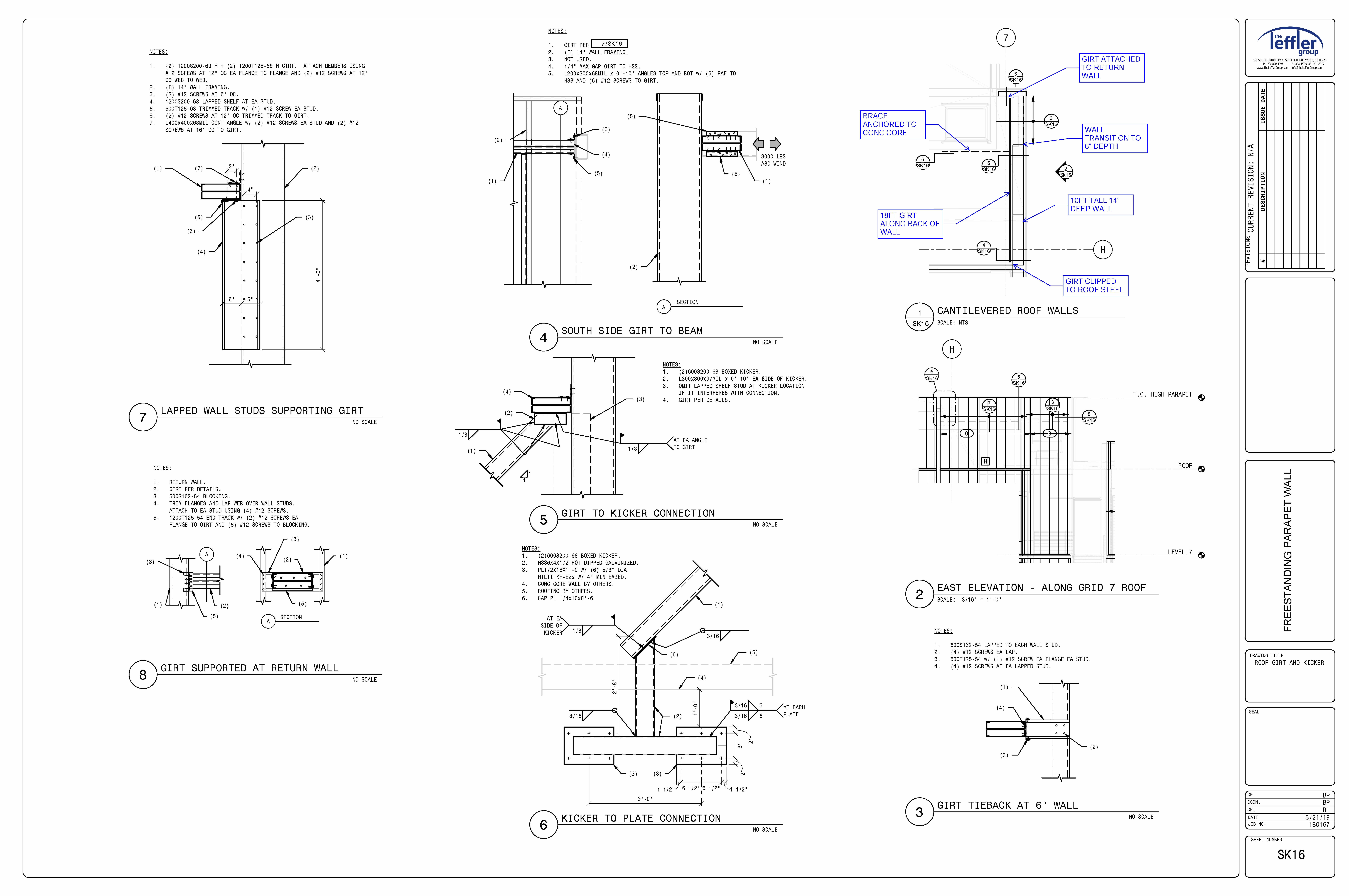
|