2022 CFSEI DESIGN EXCELLENCE AWARD WINNERS
SECOND PLACE – RESIDENTIAL/HOSPITALITY
MARTIN/MARTIN, INC. – HILTON GARDEN INN MADISON DOWNTOWN MADISON, WISCONSIN
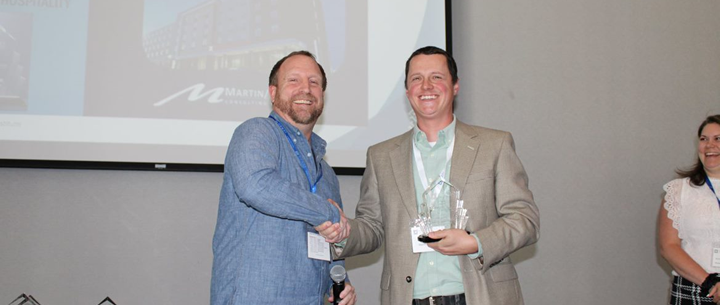
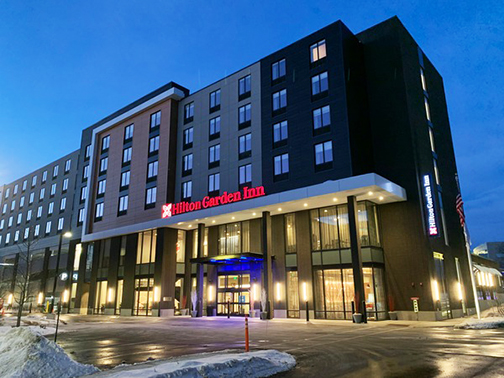
Hilton Garden Inn Madison Downtown 770 Regent Street Madison, Wisconsin 53715 Completed: February 2021 Construction Cost: $39 million
Owner:Mortenson Development, Inc. Architect of Record: Chad Bloedel, Kahler Slater Engineer of Record for Structural Work: Meghann Riedner, Graef Cold-Formed Steel Specialty Engineer: Shane Ewing, Martin/Martin, Inc. & FORSE Cold-Formed Steel Panel Fabricator: Paul Broderick, BLUvera LLC Cold-Formed Steel Specialty Contractor: Neil Wisker, Mortenson Construction Award Entry Submitted by: Grant Doherty, Martin/Martin, Inc
Project Background
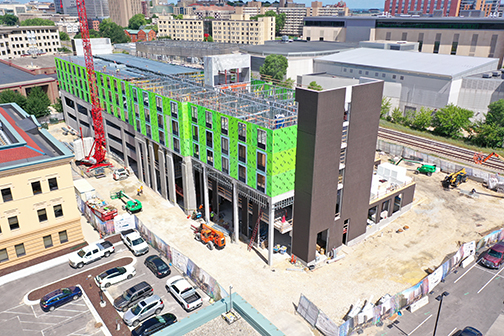
The Hilton Garden Inn Madison Downtown is a six-story hotel with four levels of guest room spaces over the split two-level hotel amenities and three-level parking precast podium. The hotel is ideally located to serve the nearby University of Wisconsin campus.
The structural system above the podium was selected to be a long-span slab on dovetail metal deck, spanning from demising wall to demising wall overload-bearing, cold-formed steel (CFS) framing.
Aside from the precast concrete stair and elevator cores, Martin/Martin was responsible for the structure above the podium. Martin/Martin also modeled all CFS framing and produced panel drawings and fabrication data for our fabricator client, BLUvera (a FrameCAD roll-form fabricator).
Design Challenges and Solutions
Martin/Martin was engaged early in the design process by BLUvera, and our “delegated” design scope was actually performed integrally with the full design team. The Mortenson-BLUvera-Martin/Martin team have worked successfully on a number of projects in a similar manner.
A few of the unique challenges/details to the project were:
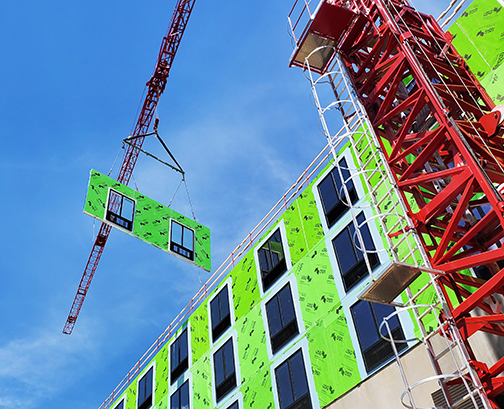
- Supporting the long-span slab on metal deck at rated shafts, interrupting load-bearing demising walls. This was achieved with a steel ledger angle attached to stud packs.
- Providing cold-formed support for roof tie-off anchors. These were not only resisted by CFS framing but were built integrally with the wall panels in the shop.
- Providing CFS framing to support a double-cantilevered canopy in Wisconsin snow drifts.
- Providing engineering, modeling and panel drawings to accommodate wall panels that were pre-sheathed and had windows installed in the shop.
- Including slab beam alternate detail that utilizes back-to-back angles. This eliminated deck forming and shoring.
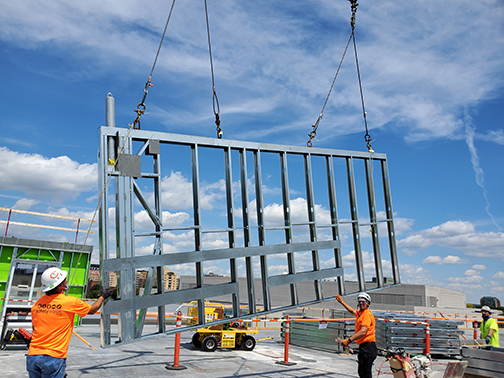
One of the more unique aspects to the project was the CFS design delivery method. While the CFS scope was considered a delegated design, the Martin/Martin team worked integrally with the design and construction teams throughout the development of the contract documents. Collaborating as an integrated design team allowed us to work through complicated details in real time rather than trying to make changes after construction documents were already completed. Having delegated design drawings completed at the same time as construction documents also saved weeks in the overall project schedule.
Martin/Martin modeled all CFS framing during this time, allowing full building information modeling (BIM) coordination with the other design disciplines and trade partners. This exhaustive effort resulted in very few clashes and issues during installation of wall panels and other trades.
|